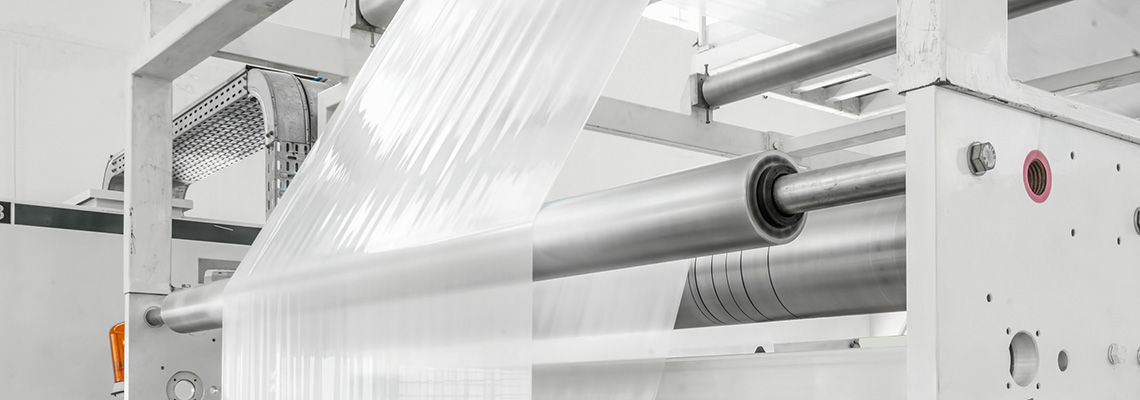
The production of bio-based PP is currently still in the development stage. Therefore, this packaging material is shown slightly differently from the previous scheme. An assessment will not be made. Bio-PP is not listed in the overview of materials with the respective assessment.
The plastic polypropylene (PP), which is known in different variants, is produced from a detailed technically controlled polymerisation reaction of the building block (= monomer) propylene (also called propene), of which it is made. Mineral oil-based propylene is obtained from crude oil (refining and thermochemical splitting) or natural gas (processing of the fractions). In addition, other forms of synthesis are also established. Asia accounts for a good 50% of the growing demand and the EU for 15% of global production. PP is the second most common plastic in the world after polyethylene (PE) with a global production volume of about 75 million tonnes. There are thermoplastic film and injection moulding variants which are processed to create a huge number of products (packaging, e.g. food films or closures and heat-stable containers; textile / technical fibres, moulded parts for consumer goods or in the construction and automotive sectors). The polymer is highly versatile and resistant.
Bio-based propylene does not occur in nature, but it can be produced from various biogenic sources by chemical transformation. Since 2019, the Finnish group Neste has been providing its partners LyondellBasell in Wesseling (D) and Borealis in Kallo and Beringen (B) with so-called “bio-naphtha” (hydrogenated vegetable oils, largely from used fats or non-food oils). LyondellBasell offers potential customers an approx. 30% bio-based PP variant produced from this (scale: 5-10 kt per year). The available variants of the product originating from a batch operation can be requested from LyondellBasell in Wesseling. With growing demand, higher percentages of biogenic raw materials are also possible; the volumes can potentially become significantly larger.
Borealis also launched a PP containing a percentage of bio-based materials at the end of 2019 (no official data on biogenic C content to date).
Depending on how these processes and approaches develop, bio-based percentages of up to about 75% are possible in the next three years. Depending on the bio-based percentage and market conditions, a significant price premium (in the order of 50–100%) can be expected. In future, the additional costs could also be reduced by offsetting them against a CO2 emission price or through plastic tax rebates. These models are conceivable, but not expected in the short term.
PP is similar to polyethylene in its properties, structure and processability and comes very close to high-density PE (HDPE) as a thermoplastic. However, PP is somewhat harder and more heat resistant. You can find further information in the CAMPUS materials database.
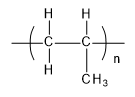
Kontakt
Both companies listed here receive the bio-based raw material from the Finnish group Neste according to their respective requirements.
According to the US-American standard ASTM D 6866 and/or ISO 16620, part 1 – 3, the bio-based carbon content can be determined and certified analytically and by calculation.
LyondellBasell offers potential customers an approx. 30% bio-based PP variant produced from this (scale: 5-10 kt per year). The available variants of the product originating from a batch operation can be requested from LyondellBasell in Wesseling. With growing demand, higher percentages of biogenic raw materials are also possible; the volumes can potentially become significantly larger. The plastic produced in this way is marketed under the product name Circulen and is approved for the manufacture of food packaging. The proportion of bio-based carbon in the plastic is detected using radiocarbon analysis. In June 2021, LyondellBasell and Neste announced an agreement for long-term cooperation in this area.
Borealis in Kallo and Beringen (Belgium) also launched a PP containing a percentage of bio-based material at the end of 2019. To date, there is no official information on the biogenic C content.
As the material has only been on the market for a few months, no information can be given at this stage.
In all probability, most of the converters mentioned under bio-PE can also process PP or bio-based PP. In addition, all plastics companies that manufacture packaging from fossil-based PP can use the (partially) bio-based variants in their production. For contact with food, the material must have the appropriate approval.
PP is one of the most frequently used packaging materials for food packaging – due to its favourable price combined with a comprehensive performance profile.
It is important to note that special pre-treatments are required for gluing and printing, while sealing is generally straightforward. Applications include films, often as composite films and bags (also suitable for MAP). The blow moulding process is used to produce hollow bodies such as bottles and containers, as well as cups, e.g. for dairy products (also by deep drawing). PP is also suitable for sterilisable packaging.
Films/bags: all types of film packaging, e.g. bags for frozen and chilled products (suitable for MAP)
Cups: all types of container packaging, trays, cosmetics
Bottles: cosmetics, beverages, detergents and cleaning agents, chemicals
Other applications: closures, canisters, tubes
PP is resistant to almost all polar solvents, acids, alkalis, water and alcohol. It has a good temperature resistance and can be processed in a wide temperature range. The properties of the plastics can be consulted in the CAMPUS® materials database for plastics.
Bio-based propylene does not occur in nature, but it can be produced from various biogenic sources by chemical transformation. Since 2019, the Finnish group Neste has been providing its partners LyondellBasell in Wesseling (D) and Borealis in Kallo and Beringen (B) with so-called “bio-naphtha” (hydrogenated vegetable oils, largely from used fats or non-food oils). LyondellBasell offers potential customers an approx. 30% bio-based PP variant produced from this (scale: 5-10 kt per year). The available variants of the product originating from a batch operation can be requested from LyondellBasell in Wesseling. With growing demand, higher percentages of biogenic raw materials are also possible; the volumes can potentially become significantly larger.
Borealis also launched a PP containing a percentage of bio-based materials at the end of 2019 (no official data on biogenic C content to date).
Depending on how these processes and approaches develop, bio-based percentages of up to about 75% are possible in the next three years. Depending on the bio-based percentage and market conditions, a significant price premium (in the order of 50–100%) can be expected. In future, the additional costs could also be reduced by offsetting them against a CO2 emission price or through plastic tax rebates. These models are conceivable, but not expected in the short term.
Sustainability criteria

1. Ecology


For the ecology criterion, seven sub-criteria (parameters), which are considered essential for organic food production, have been included in the assessment: land use/competition for food, environmental compatibility, certifications (cultivation and processing), genetic engineering, disposal (recycling, composting), life cycle assessments and bio-based content.
The raw materials that can be used for the production of bio-based PP in processes already available today are manifold. Bio-Naphtha from Neste can be produced from a variety of (plant) oil-containing sources. The raw materials are usually ISCC PLUS certified and thus precisely defined in terms of their composition and cultivation or process chain. As Neste generally does not use freshly produced food oils, but by-products or waste, there is very little impact on land use and all other agriculturally dominated life cycle assessment indicators.
Since the process of propylene and polypropylene production, as well as the application services and disposal options for bio-based and fossil-based variants, are identical, it is solely the “environmental rucksack” of the raw materials which is decisive for the expected future differentiation in terms of the life cycle assessment. Due to the binding of CO2 from the atmosphere from plant-based raw materials, bio-PP can also be expected to have a general advantage in terms of the indicators CO2 emissions (climate protection) and consumption of fossil raw materials (resource protection) compared to mineral oil-based raw materials. For other indicators, there will be positive and negative comparison results, which would then have to be weighted individually.
In May 2020, Utrecht University published a study with a life cycle assessment of bio-PP made from used cooking oils. This study was prepared as part of a major EU biofuel study.
On a standardised and weighted basis, the environmental impacts of PP produced from used cooking oils are dominated by climate change (28%), the use of fossil resources (23%) and water consumption (11%). The following environmental hotspots were identified: the polymerisation process (38%), hydrogen production (21%), LPG production (18%) and LPG combustion (8%). Compared to petrochemical PP, PP produced from used cooking oil can achieve impact reductions of 40–62% for climate change and 80–86% for fossil fuel resource use from the cradle to the factory gate, depending on the allocation approach chosen. For other impact categories, the environmental footprint of bio-based PP is strongly influenced by the choice of the allocation method.
Bio-Naphtha from Neste can be produced from a variety of (plant) oil-containing sources. The raw materials are usually ISCC PLUS certified and thus precisely defined in terms of their composition and cultivation or process chain.
Currently, no cooking oils are produced from genetically modified oil plants in Europe. For this reason, the probability of introduction into the raw materials for the bio-naphtha from Neste is currently seen as very low at best.
Bio-based PP has the same recycling properties (drop-in solution) as conventional PP and can therefore be recycled together with it without any problems.
However, it should be noted that, although the PP recycling system is well developed in itself, many PP films are not recycled, but instead used for thermal recycling (incineration). This applies especially to films < 2 x 2 cm. Incineration of biomass-based PP is possible. It is stable when disposed of in a landfill and is not biodegradable.
In May 2020, Utrecht University published a study with a life cycle assessment of bio-PP made from used cooking oils. This study was prepared as part of a major EU biofuel study.
On a standardised and weighted basis, the environmental impacts of PP produced from used cooking oils are dominated by climate change (28%), the use of fossil resources (23%) and water consumption (11%). The following environmental hotspots were identified: the polymerisation process (38%), hydrogen production (21%), LPG production (18%) and LPG combustion (8%). Compared to petrochemical PP, PP produced from used cooking oil can achieve impact reductions of 40–62% for climate change and 80–86% for fossil fuel resource use from the cradle to the factory gate, depending on the allocation approach chosen. For other impact categories, the environmental footprint of bio-based PP is strongly influenced by the choice of the allocation method.
Depending on how these processes and approaches develop, bio-based percentages of up to about 75% are possible in the next three years.
LyondellBasell offers potential customers an approx. 30% bio-based PP variant (scale: 5-10 kt per year). The available variants of the product originating from a batch operation can be requested from LyondellBasell in Wesseling. With growing demand, higher percentages of biogenic raw materials are also possible; the volumes can potentially become significantly larger. The plastic produced in this way is marketed under the product name Circulen and is approved for the manufacture of food packaging. The proportion of bio-based carbon in the plastic is detected using radiocarbon analysis.
Borealis in Kallo and Beringen (Belgium) also launched a PP containing a percentage of bio-based material at the end of 2019. To date, there is no official information on the biogenic C content.
PP is also increasingly frequently used in material composites; in this case, the bio-based content of the total material composite is to be taken into account.
2. Social compatibility

For the social compatibility criterion, the assessment refers to the existence of social standards in processing. These can be internationally valid guidelines, national legal standards or private sector standards. The social standards of the country from which the raw material originates or in which the processing takes place are used as a basis for the assessment.
The collection of vegetable oils and especially the processing into PP is carried out in EU countries. Thus, the social standards in the EU apply.

3. Safety and technology
Safety and technology
With the safety criterion, the focus is on safety for the consumer. Here, it is mainly migration potential which is considered. Regarding technology, the technological processability of the packaging material is evaluated. Highly extensive data is available for biomass-based packaging materials made of the same material, such as bio-PP, as these have the same properties as the equivalent fossil-based plastics.
Bio-PP has properties comparable to mineral oil-based PP, whereby there are many variants of PP for a wide range of applications. PP is an inexpensive mass product, although somewhat more expensive than PE, which is physiologically non-hazardous and practically odourless and tasteless. That is why it is widely used in the food industry. Compared to PE, PP offers improved barrier properties, which are significantly enhanced by an EVOH layer in cases of higher requirements. The mechanical requirements of bio-PP are comparable to those of mineral oil-based plastics but should be tested individually due to the large number of available types.
4. Quality

The quality criterion encompasses the legal requirements for packaging material.
In the BfR database “BfR Recommendations on Food Contact Materials“, the recommendations for polypropylene are summarised under the serial number 070. The legal requirements are defined in the “Regulation on plastic materials and articles intended to come into contact with food” (Regulation (EU) No 10/2011).
For special applications with a high migration potential, an individual risk assessment should be carried out for PP as well for bio-PP.
Similar to PE, PP is a versatile packaging material that offers advantages in terms of stiffness and temperature resistance. Protective gassing without a coating can only be implemented under certain conditions.
In public perception, non-biodegradable plastics such as PP, which accumulate in the environment, are viewed very negatively – especially with regard to microplastics. On the other hand, the already existing recycling possibilities are a positive aspect.
Pre-treatment is required for printing and gluing. Bio-based PP is just as stable as mineral oil-based PP. PP can be stored for a very long time.
Highly extensive knowledge exists regarding different applications for polypropylene. The (partially) bio-based variants of PP available for packaging material do not differ physically or chemically from those made of fossil-based PP. This also applies to the recyclability, compatibility with recycling processes or mixtures of conventional PP with bio-based or recycled PP.