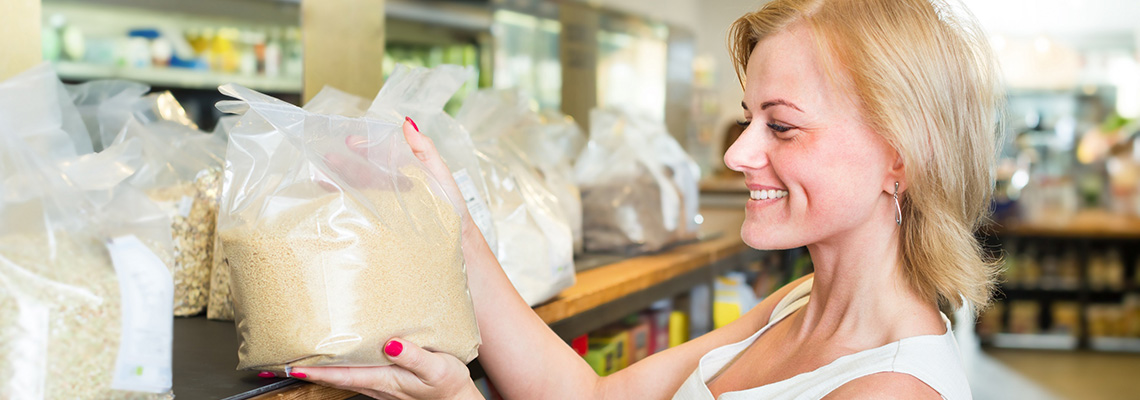
Polyethylene terephthalate (PET) is a thermoplastic material used for bottles, films and textile fibres. PET belongs to the polyester group.
It consists of 70 percent terephthalic acid and 30 percent monoethylene glycol (MEG) by weight and is frequently used in the packaging sector. For bio-PET, MEG is produced from renewable raw materials from plants instead of fossil raw materials.
Bio-PET is made using sugar cane from Brazil
Bio-MEG is made using ethanol from sugar cane. According to a study by the IFEU Institute commissioned by the Federal Ministry of Food and Agriculture, it is approximately 20–40% more expensive than conventional PET. The ethanol produced from Brazilian sugar cane forms the starting point for the production of monoethylene glycol (MEG).
Bio-PET has many positive characteristics
Bio-PET can be introduced into the existing recycling system as a drop-in solution. The long-term goal is to produce a completely bio-based PET bottle, for which the terephthalic acid is also obtained from renewable raw materials. PET is a material with high breaking strength and medium barrier properties. PET is not resistant to strong inorganic acids.
The recycling of PET is practised on a large scale and takes place using various processes available on the market. These processes are designed to produce bottles from recycled material which are also intended for use in the food industry. This saves about 60 percent of the energy compared to producing new bottles.
The material PEF (polyethylene furanoate) represents a further development. However, although it has been announced time and again, it is not yet technically available on the market. This material is to be based 100% on renewable raw materials and is to be superior to conventional PET products in terms of weight, barrier and thermal properties.
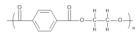
Symbol-Legende
positive evaluation
Evaluation in individual cases
predominantly critical evaluation
Kontakt
Teijin
Teijin is a global manufacturing company that produces bio-PET mainly for textile and automotive fibres. The fibre is sold as ECO CIRCLETM plant fibre.
Joint Venture Corpus Christi Polymers
The know-how regarding bio-MEG production using PRODESA® technology from the Mossi Ghisolfi Group has been sold to Alpek Polyester, Indorama Ventures and the Far Eastern New Century Corporation. These companies intend to jointly launch production of the bio-PET component MEG in Texas (USA) in the joint venture Corpus Christi Polymer. The raw materials for this will come from their own agricultural land.
ALPLA Werke Alwin Lehner GmbH & Co KG
ALPLA is a company founded in 1955 in Hard (Austria), which now has over 150 locations in more than 40 countries. With its commitment to PET recycling, it implements its goals of increasing the proportion of recycled material in bottles. In the six most important plants, this is already at 35 percent.
Coca-Cola Erfrischungsgetränke AG
Coca-Cola sells a bottle produced partly from plant-based raw materials under the name PlantBottle™. By mass, the bio-based percentage is between 14 percent (with 25 percent recycled PET in the PlantBottleTM PET) and 30 percent (without recycled PET in the PlantBottleTM PET). Other companies also use bio-PET for bottling soft drinks and water.
Bio-PET is now available through various converters. Coca-Cola uses the PlantBottle™ for VIO bottles. According to Coca-Cola, the percentage is around 14% for this brand. Since 2009, over 25 billion PlantBottle™ units have been produced worldwide. The current annual capacity of bio-PET in 2019 is approx. 200,000 tonnes, which corresponds to 9.8% of the share of bioplastics.
Bio-PET packaging materials are produced from the granulate at various locations. The raw material bioethanol for the production of bio-MEG currently comes from sugar cane and bagasse (a by-product of sugar cane production) from Brazil (about 80 percent) and from bagasse from Indian sugar cane production (about 20 percent). European sugar beet could also be used as a raw material. Their use is subject to economic criteria and current availability.
To date, over 25 million PlantBottleTM units have already been produced at various locations in Europe (Denmark, Benelux, Norway, Sweden), USA, Canada, Brazil, Mexico, Chile and China. The bottle sizes produced are 0.33 litres, 0.5 litres, 0.75 litres and 1.5 litres. The PET successor material PEF is being tested on a pilot scale in collaboration with the companies Avantium, Coca-Cola, Danone and ALPLA. It will be several years before commercial production takes place.
FKuR Kunststoff GmbH
FKuR is a bioplastics specialist with a broad portfolio of bio-based plastics. The raw material basis is plastic granulate. The company’s headquarters and production site are located in Germany. As a European distribution partner, FKuR sells bio-PET under the brand name GLOBIO. GLOBIO is a drop-in solution for granulate and can replace conventional PET in a variety of applications. Typical fields of application for GLOBIO in the food industry are bottles, films and thermoformed items.
FKuR also offers other product lines (Bio-Flex®, Biograde®, Fibrolon®, Terralene®) for an extensive range of applications. In addition to its own raw materials, FKuR sells bio-based raw materials from various manufacturers (bio-PE from Braskem, bio-PET from Toyota Tsusho, bio-PA from Evonik).
Apart from the various application methods and material properties on the websites of the manufacturers, an additional, very important data source for the material properties of biopolymers and the packaging materials produced from them is the biopolymer database of IfBB Hannover (Institute for Bioplastics and Biocomposites, Hannover University of Applied Sciences and Arts) and the company M-Base GmbH.
Foils/bags: For various product applications; multilayer systems or coatings are used for special barrier requirements; cups, tins, thermoforming applications: for dry, fresh and paste-like food (e.g. fresh meat).
Bottles: Various beverages, mainly soft drinks, fruit juices and water, made from preforms. Larger containers can also be made of PET.
Other applications: PET barrels for beer up to 40 litres; also for hot filling if pre-stretching is used; packaging for cosmetics
PET has high tensile strength and high mechanical stability. As a colourless film with high transparency, it is versatile and offers a wide range of application possibilities. The barrier properties are in the mid-range and are improved using coatings or multilayer systems. Beer and wine can now also be filled into PET bottles, as the barrier properties have been significantly improved.
Material consumption and costs are low because very thin films can be produced with PET.
Currently, only the monoethylene glycol (MEG) is bio-based in bio-PET, which means that the total bio-based material content reaches up to 30 percent. Thanks to special processing methods, recycled PET can also be used for food applications. Combining recycled PET and bio-PET (such as in Coca-Cola’s PlantBottleTM) reduces the proportion of bio-based materials.
Sustainability criteria
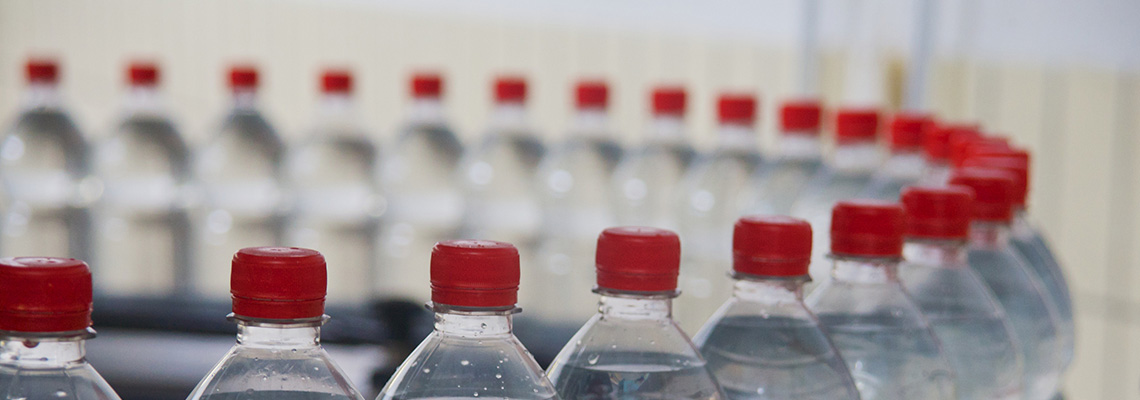
1. Ecology


For the ecology criterion, seven sub-criteria (parameters), which are considered essential for organic food production, have been included in the assessment: land use/competition for food, environmental compatibility, certifications (cultivation and processing), genetic engineering, disposal (recycling, composting), life cycle assessments and bio-based content.
After Colombia, Brazil has the most efficient and productive sugar and bioethanol production infrastructure in the world with by far the highest production volume. At present, sugar cane is the main raw material used to produce the bio-based component of bio-PET.
The production of one tonne of bio-PET with an assumed bio-based percentage of 100 percent would have a land consumption of 0.31 hectares and thus an average land efficiency compared to the production of one tonne of PLA and the production of one tonne of bio-PE.
Bio-based PET, PE and PLA can be produced from sugar cane and also have similar applications.
The processing routes for the production of bio-PET from sugar cane can be viewed here.
Note: PET bottles have a high recycling rate of over 90 percent in Germany.
Sugar cane is cultivated as the raw material for the production of bio-PET.
Cultivation of sugar cane in Brazil
Sugar cane is a perennial plant with stems up to seven metres high and five centimetres thick and sugar-storing pith (7–20 percent sucrose). It has high requirements where heat (optimum: 25 to 28 degrees), water (optimum: 1,200 to 1,500 mm of precipitation) and nutrients are concerned, and is often grown as a monoculture for perennial use (2 to 10 years). Depending on the location, variety and cultivation conditions, the plants require 80 to 200 kilograms of nitrogen per hectare and up to 350 kilograms of potassium per hectare. The use of synthetic fertilisers is reduced via the use of by-products. Phosphate fertilisation is of less importance. Sugar cane has a fungal flora that increases the absorption of phosphate. Sugar cane is harvested by hand or by machine. However, the proportion of manual labour will decrease in the future (cf. section on “Biodiversity/Air pollution”).
Sugar cane is a robust crop, generally grown on the same land for five consecutive years.
Water consumption
In Brazil, sugar cane is grown mainly in the central-southern part of the country, where the high rainfall almost always allows it to be grown without irrigation. Water is mainly consumed in the processing of sugar cane. A considerable amount is needed for cleaning the raw product.
Energy consumption
In general, ethanol production requires a lot of energy. However, the use of heat and electricity generated during the production process by burning bagasse (co-product of the grinding process in ethanol production) covers a large portion of the energy needs. Most of the sugar cane mills are therefore self-sufficient in terms of energy. The bagasse is used as an energy source for electricity generation. Surplus electricity is fed into the local power grid.
Biodiversity/Air pollution
The burning of sugar cane fields is harmful to the atmosphere and biodiversity. It makes harvesting easier by removing the leaves from the stalks and protecting workers from dangerous animals. Harvesting by machine without burning is more environmentally friendly but is detrimental to jobs.
Cultivation of sugar cane in Brazil
The main sugar cane growing area is the State of São Paulo. Brazil has a strict regime regarding the regulation of sugar cane cultivation and nature conservation. Several laws have been enacted to control the cultivation of sugar cane. The rules established by Agro-Ecological Zoning apply nationwide. These laws are not always observed, and land is still classified as “degraded” because it can then be used for agricultural purposes. Braskem follows stricter rules.
At Coca-Cola, various certifications are available and can be requested directly from the company. Coca-Cola is a member of Bonsucro.
Indian bioethanol is produced by processing a by-product (molasses) of sugar extraction from sugar cane. The use of the waste material was implemented at the request of the WWF and the Indian government but plays a subordinate role in terms of quantity.
Coca-Cola uses sugar cane from Brazil and sugar cane molasses from India.
According to Braskem, no genetically modified plants are currently used on Brazilian plantations. The ISAAA (International Service For The Aquisition Of Agri-Biotech Applications) database also does not list any cultivation of GM sugar cane in Brazil or India, keyword “raw material profile”.
Bio-based PET has properties identical to conventional PET in terms of recycling (drop-in solution) and can therefore be easily recycled together with it. The PET recycling quota for beverage bottles in Germany is over 90 percent.
Coca-Cola states that the proportion of recycled PET in the production of new PlantBottleTM bottles in Germany is around 25 percent.
According to the IFEU study “Biobasierte Kunststoffe als Verpackung von Lebensmtiteln“ (Bio-based plastics as packaging for food products), PET mono films and thermoformed trays for food packaging are currently only recycled to a moderate extent in Germany. PET composite films can only be thermally recycled.
Due to its low weight and good recycling properties, PET generally has a positive environmental footprint compared to other beverage packaging materials. Carbotech recommends PET for beer, fruit juices, other sweet drinks or carbonated beverages due to its life cycle assessment and material properties. Other materials are recommended for milk or wine.
Coca-Cola is working with Braskem on raw material sourcing and life cycle data research on Brazilian sugar cane. These data are determined for ethanol produced from Brazilian sugar cane from the “Centre-South” region.
An unpublished LCA from 2013/2014 is available. It covers Brazilian bioethanol and its processing into bio-MEG in India.
Currently, only the monoethylene glycol (MEG) is bio-based in biomass-based PET, which means that the bio-based content of the total material is between 14 and 30 percent.
Coca-Cola refers to the PET beverage bottle made of bio-PET as PlantBottleTM. The PlantBottleTM is recyclable, just like other PET beverage bottles.
2. Social compatibility

For the social compatibility criterion, the assessment refers to the existence of social standards in cultivation and processing. These can be internationally valid guidelines, national legal standards or private sector standards. The social standards of the country from which the raw material originates or in which the processing takes place are used as a basis for the assessment.
The assessment must be specific to each production area and producer.
Coca-Cola tests according to “SGP”
Coca-Cola has established Supplier Guiding Principles (SGPs), which require that workplace conditions at least comply with local labour laws and key international conventions. The SGPs are audited by independent third parties. Part of the assessment is confidential interviews with local employees and contract workers.
It has not yet been possible to certify sugar cane cultivation in India according to Bonsucro. Therefore, Coca-Cola uses waste from the sugar cane process (molasses) in this case. With regard to the use of waste from this process for the production of bio-MEG (a bio-based component of PlantBottleTM), a partnership has been established with the main supplier from India. The aim of the partnership is to get in contact with local sugar suppliers in order to guarantee that no human rights violations occur in the supply chain. This partnership is intended to provide an overview beyond the direct suppliers (chemical companies), extending to mills and farmers.
In Brazil, Coca-Cola is working with the WWF to familiarise key sugar suppliers with the Bonsucro standard and push them towards certification.
According to Coca-Cola, if migrant workers are employed, local labour rights and central international conventions must be respected.
Coca-Cola produces at many sites around the world and must therefore comply with the social standards applicable in each country. Various certifications are available and can be requested directly from the company. Coca-Cola is a member of Bonsucro.
3. Safety and technology


With the safety criterion, the focus is on safety for the consumer. Here, it is mainly migration potential which is considered. Regarding technology, the technological processability of the packaging material is evaluated.
Highly extensive data is available for biomass-based packaging materials made of the same material, such as bio-PE, bio-PP and bio-PET, as these have the same properties as traditional plastics.
It is known that small amounts of acetaldehyde and antimony can migrate from PET. However, the quantities detected so far are below the limits defined by Regulation (EU) No 10/2011. With regard to petroleum hydrocarbons, PET offers good barrier properties.
The German Federal Institute for Risk Assessment (BfR) has defined specifications for use as food packaging.
Very good barrier properties can be achieved using coatings, which also significantly improve the shelf life of products packaged in PET.
There are various recycling technologies for PET for which a Food and Drug Administration (FDA) approval exists. Gneuss has developed a process for which FDA approval has been granted without pre-treatment or post-treatment of the material.
A wide range of films
PET films are widely used for various applications in the food sector. Individual solutions adapted to the respective packaging scenario are made possible by using different processing methods and coating systems. The gloss and transparency of the films are very good (low yellowing value), even if they are based on recycled materials. The films are available with a very wide range of properties.
Application for containers possible
An oxygen absorber is also added for special product applications. Overall, very good barrier properties are achieved using coatings.
Processing can be carried out on the traditional processing machines for fossil-based PET. There are no additional requirements for bio-PET.
PET has good barrier properties, which can be significantly improved by additional coatings and multilayer applications. This allows most of the applications in the food sector to be covered.
PET is produced using a wide variety of methods for the corresponding applications. In order to minimise material expenditure and costs, it should be precisely defined which requirements the material must fulfil for the planned application.
4. Quality


The quality criterion encompasses the legal requirements for packaging material. According to the German Federal Institute for Risk Assessment (BfR), “quality” means compliance with the legal requirements and BfR specifications for packaging. Ecological and environmental aspects are important criteria for bio-based packaging. The packaged product results in specifications which the packaging material needs to fulfil and which should be precisely defined in advance. In many cases, excessive requirements lead to elaborate, expensive and unsustainable packaging. Consumers also demand transparent and sustainable packaging with the same usage properties. Due to the identical composition of the packaging material, bio-PET can reduce the use of mineral oil-based packaging solutions made of PET in many cases.
PET is approved for the packaging of foodstuffs. For PET, the legal requirements are defined in the “Regulation on plastic materials and articles intended to come into contact with food” (Regulation (EU) No 10/2011).
Even recycled material can be reused for the packaging of foodstuffs by means of certain reprocessing techniques.
Due to its versatile properties (e.g. high strength, low weight and medium barrier properties), PET is used for a wide range of applications (cans, bottles, e.g. for soft drinks; films, e.g. pouch packaging for cosmetics and food).
The availability of plant-based PET packaging is still low. In this case, larger quantities are required in order to implement economically viable packaging ideas. By using barrier layers, the processing and/or barrier properties can be improved.
Monofilms made of A-PET (amorphous) are offered, which can be used in a wide temperature range. They are mainly used for thermoformed transparent containers. C-PET (crystalline) has a high crystallinity with a very high melting point (> 280 °C). These packages have a very good gloss and very high transparency. They are also suitable for use in microwave and convection ovens. C-PET can also be used for hot fillable beverages. In addition, there are duplex films, triplex films and composite films for a wide range of applications.
The consumer requirements regarding safe packaging are guaranteed. Due to the versatile design possibilities, a great many customer requirements can be implemented.
Particularly worth mentioning is the high mechanical stability despite the low weight.
With regard to consumer requirements, the low bio-based content of 15-30 percent and the limited availability must be taken into account. Furthermore, non-biodegradable plastics such as PET, which accumulate in the environment, are viewed very negatively – especially with regard to microplastics. On the other hand, the already existing recycling possibilities are a positive aspect.
The product is extremely stable and has a nice shine and high transparency. It is extremely versatile.
PET packaging can be printed on in many ways. Multilayer films can be used to create very attractive and versatile packaging. In addition, there are numerous applications for lids, as PET can be shaped in a great many ways.
The product is extremely stable and has a nice shine and high transparency. It is extremely versatile.
PET packaging can be printed on in many ways. Multilayer films can be used to create very attractive and versatile packaging. In addition, there are numerous applications for lids, as PET can be shaped in a great many ways.
Further developments such as the bioplastic PEF (polyethylene furanoate) would make it possible to achieve significantly higher bio-based percentages with even better processing properties.
The disadvantages are the currently still very high price and the small quantities available to date from experimental production.
One other development is the production of biodegradable PET by the company Resilux.