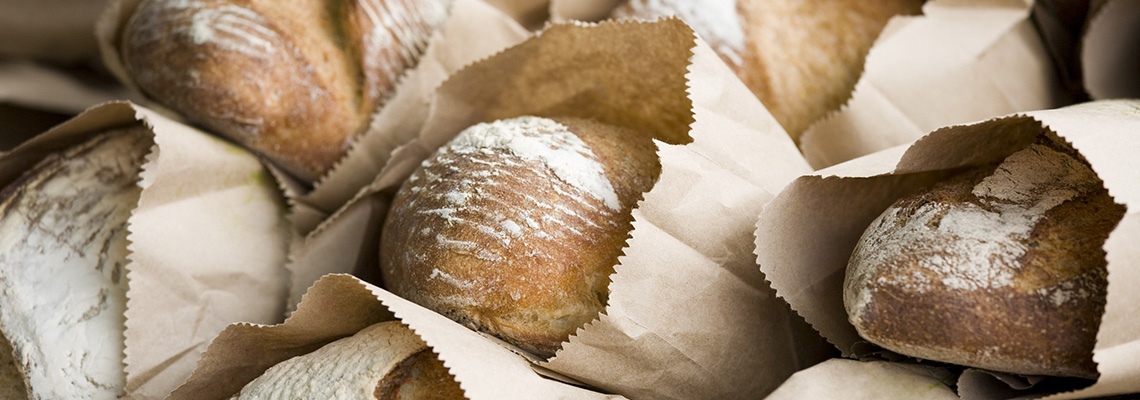
Polylactide (PLA) is produced by polymerising lactic acid obtained from raw materials containing starch or sugar. The process is now much cheaper and requires less energy than it did years ago. Milk of lime is used as a neutralising agent, resulting in large quantities of gypsum, which is used in agriculture. The monomers used in the production of PLA can be in both D and L form, resulting in very different processing conditions and areas of application.
The largest manufacturer, NatureWorks, produces PLA from genetically modified maize in Blair (USA). In recent years, various manufacturers around the world have set up additional production facilities. A European non-GMO alternative is offered by Total Corbion PLA (headquartered in Gorinchem, Netherlands). It produces lactic acid, lactide and PLA in Rayong (Thailand). The raw material used is mainly sugar cane from Thailand. The use of other raw materials is planned.
Prices and designation of PLA
In the next two to five years, larger price reductions are only conceivable for PLA if new and significantly cheaper raw materials can be obtained or more cost-effective manufacturing processes are developed. A further increase in production capacity is possible, but significant cost reductions can only be expected from cheaper raw materials.
Note: When the term PLA is used in this tool, PLA blends (all mixtures containing PLA) are also included.
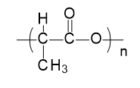
Symbol legend
positive evaluation
Evaluation in individual cases
predominantly critical evaluation
Kontakt
Total Corbion PLA
Corbion is a global company with production sites in the US, Brazil, Europe and Thailand. It produces lactide and lactic acid, which are polymerised by partner companies. Only GMO-free raw materials are used for the production of the monomers.
PLA with higher heat stability (up to 180 °C/HDT/A) is offered by Corbion together with Sulzer Chemtech AG. There are various test plants as well as smaller production facilities. The PLA is made from Thai sugar cane and produced in Rajong (Thailand). According to Total Corbion, another plant is to be built in France with an annual capacity of about 100,000 t for the production of PLA. Approximately 300,000 tonnes of lactic acid will be produced annually at various sites worldwide.
The quantities of PLA produced by partner companies are significantly lower.
Jilin Cofco Biomaterial Corporation
This Chinese company performs production using “PLAneo” technology. This is done through a collaboration with Thyssenkrupp.
Currently, Thyssenkrupp has another PLA plant under construction in China.
NatureWorks belongs to the parent companies Cargill (USA) and PTT Global Chemical (Thailand). They produce their “Ingeo” using maize from the USA (Blair, Nebraska). The annual capacity is 150,000 tonnes.
Among other applications, their PLA is used for packaging for fresh foods with a shelf life of up to four weeks, e.g. for fresh dairy products and/or cheese. PLA is used to make yoghurt pots, cutlery, drinking cups, trays for ready-to-eat salads and/or tomatoes and packaging for vegetables and fruit. The packaging is high-gloss and transparent. NatureWorks offers about 20 different types of PLA for various applications, and combinations with Innovia’s NatureFlex™ film are also possible.
Uhde Inventa-Fischer is an international plant builder and licensor that operates a PLA pilot plant in Guben (Brandenburg, Germany) with an annual capacity of 500 tonnes. The plant is used for process and product optimisation, as well as for the production of material samples for potential customers. The plant processes the raw material lactic acid, which is produced in a pilot plant of the parent company ThyssenKrupp Industrial Solutions AG using renewable raw materials. Uhde Inventa-Fischer has patented processes covering the entire production chain, i.e. from the production of LA and lactide to the bioplastic PLA. In 2018, a plant with a production capacity of 10,000 tonnes was put into operation at Cofco in China.
BASF is a German chemical company with a biodegradable plastics division. It produces the material ecovio®, which consists of ecoflex® and PLA produced by BASF. Ecoflex® F is based on a fossil polyester (PBAT), while the FS variant is produced using (among other things) vegetable oil which does not compete with food production. The processing capacity for ecovio® and ecoflex® is 75,000 tonnes.
BioPak Pty Ltd
BioPak is an Australian manufacturer of cups, bowls, containers, cutlery, plates and plastic bags made of PLA from NatureWorks.
BIOTEC GmbH & Co. KG (benannt als BIOTEC)
BIOTEC is a German manufacturer specialised in compostable plastics made from starch blends. The raw material basis is potato starch and in part also other biodegradable plastics. In addition, the company also produces fully biodegradable thermoplastic plastic blends based on PLA, PHA (polyhydroxyalkanoates) and PBAT (polybutylene adipate terephthalate). Depending on the customer’s requirements, the PLA comes from various sources, including GMO-free sources. PHA is used to produce injection moulded items such as coffee capsules. Other products include containers for lipid creams and tubes for cream. In the case of water-based contents, water vapour barriers are used.
Coveris is the sixth-largest manufacturer of packaging solutions in the world, with subsidiaries in 21 countries and sales of 2.5 billion US dollars. Its products include co-extruded PLA blends for paper rolls, napkins and dust jackets (magazines, journals). The processing locations in Germany are Warburg and Halle/Westphalia.
This bioplastics specialist producing in Willich offers a broad portfolio of compostable/biodegradable and bio-based plastics. In addition to the bioplastics series Biograde® (cellulose), Fibrolon® (plastic-wood mixture) and Terralene® (PE), it also produces Bio-Flex® and PLA blends. In addition to the packaging materials it produces, FKuR sells bio-based raw materials from various manufacturers (bio-PE from Braskem, bio-PET from Toyota Tsusho, bio-PA from Evonik).
Maag is a converter (not a manufacturer) of various PLA films.
OFOTEC is a German manufacturer of films based on PP (polypropylene). Its product range also includes a PLA monofilm under the name OFO-Naturale. A bio-based PE (polyethylene) is also planned under the name OFO-Natylene.
Taghleef is a global company with several locations. It is one of the largest producers of biaxially oriented PP films (BOPP) and BOPLA films. Under the brand name “Nativia”, it offers a product range of compostable and bio-based BOPLA films for food packaging. Taghleef has a production capacity of 500,000 tonnes for BOPP, CPP and BOPLA. The Taghleef website provides numerous data sheets and specifications. Registration is required.
One very important source of data for the material properties of biopolymers and the packaging materials produced from them is the biopolymer database of IfBB Hannover (Institute for Bioplastics and Biocomposites, Hannover University of Applied Sciences and Arts) and the company M-Base GmbH.
Foils/bags: Fresh products such as vegetables, salads, bread, dry products with a short best before date (BBD), catering products
Cups/thermoforming: Meat, dairy products, desserts, chilled ready meals
Bottles: Fresh products with a short shelf life
Other applications: Windows for bread bags, coating of paper bags as a grease barrier
- Biodegradable in industrial composting, not suitable for home composting.
- Medium water vapour permeability (20–80 g/m2d, according to DIN 53122) with low other barrier properties.
- Very good transparency and high stiffness of the products. PLA is rather brittle and additives are often used as plasticisers.
- An advantage is the good aroma barrier, which is also used to protect against ink migration in tea bags, for example.
- The stability against acids, alkalis and various solvents is low.
- The good printability is an advantage.
- A copolymerisation with cyclic monomers can be carried out to improve the material properties. One application is blending with other polyesters. The addition of calcium carbonate can also result in new material properties (Omya Smart fill)
- PLA can partially or completely replace LDPE, HDPE, PP, PA, PS or PET, depending on the application. PVC shrink films and PVC cards can also be replaced by PLA.
In the USA, the raw material used is maize (glucose from maize starch), in South-East Asia, it is sugar cane. Other raw materials, such as sweet potatoes, are in the works. In Germany, there is a small pilot plant at the Fraunhofer Institute for Applied Polymer Research (IAP) where experiments are being conducted with various raw materials.
Other sources of sugar/starch include barley, cassava, wheat, potatoes, sugar beet and sago. Experiments are also being carried out with agricultural by-products or residues: with cellulose, e.g. through Cellulac, and with bagasse from sugar cane, e.g. through the Leibniz Institute for Agricultural Engineering Potsdam-Bornim (ATB). Extensive research is still needed here, as the effectiveness of the plant depends very much on the raw material.
Sustainability criteria

1. Ecology 


For the ecology criterion, seven sub-criteria (parameters), which are considered essential for organic food production, have been included in the assessment: land use/competition for food, environmental compatibility, certifications (cultivation and processing), genetic engineering, disposal (recycling, composting), life cycle assessments and bio-based content.
Currently, it is mainly maize from NatureWorks and sugar cane from Total Corbion PLA which are used for the production of PLA.
There are considerable differences in the efficiency of land use.
The land efficiency of the production of one tonne of PLA from sugar cane, which requires 0.16 hectares of land, is much better than the production of one tonne of PLA from maize (0.37 hectares).
For better comparability, the tool assumes a bio-based content of 100% in each case. PLA and (partially) biomass-based PET can be produced from sugar cane and also have similar applications. For all raw materials, yields can vary considerably from region to region.
Processing routes for the production of PLA from maize and/or sugar cane
Maize as a raw material (pure PLA)
Input: 0.37 hectares (equivalent to 2.39 tonnes of maize) → Output: 1 tonne of PLA
Please note: In the case of blends, the land requirements of all raw materials used must be taken into account.
Sugar cane as a raw material
Input: 0.16 hectares (equivalent to 11.31 tonnes of sugar cane) → Output: 1 tonne of PLA
In this context, in addition to land use efficiency, the type of land use (intensive/extensive, etc.) must also be taken into account (cf. section 1.2 on “Environmental compatibility”).
Maize and/or sugar cane is cultivated as the raw material for the production of PLA.
Maize has high nutrient requirements (especially nitrogen) and, due to its slow development when young, a low ability to compete with weeds. The high nutrient requirements can lead to increased leaching of nitrate at certain times of the year, e.g. after harvesting, or when no undersown crops have been planted to utilise the residual nitrogen. This may result in groundwater contamination with fertilisers. There are also risks of soil compaction and erosion (depending on the location and cultivation frequency). Erosion is encouraged by cultivation in rows and without undersowing.
Water consumption
Irrigation takes place depending on the location. Hardly any irrigation is performed in the state of Iowa, while partial irrigation is performed in eastern Nebraska. A survey was conducted in 2001. According to the results, 9.4 percent of the farmers who supplied NatureWorks irrigated their land (20 litres per kilogram of Ingeo or 13.6 litres per kilogram of maize (15 percent moisture content). Water consumption is not an environmental issue in itself. A lowering of the groundwater level, for example, would be problematic.
Sugar cane contains between 7 and 20 percent sucrose and requires a lot of heat (optimum: 25–28 °C), water (optimum: 1200 to 1500 millimetres of precipitation) and nutrients. It is often grown as a monoculture for perennial use (2 to 10 years). Depending on the location, variety and cultivation conditions, the plants require 80 to 200 kilograms of nitrogen per hectare and up to 350 kilograms of potassium per hectare. Phosphate fertilisation is of less importance due to fungal flora which increases phosphate uptake. Generally, sugar cane is planted three times in a row in Thailand. Sugar cane is harvested by hand or by machine. Part of the manual harvesting process involves burning. However, the proportion of manual labour will decrease in the future (cf. section on “Biodiversity/Air pollution”).
Cultivation of sugar cane in Thailand
Irrigation
In 2006, approx. 87 percent of the sugar cane farmers produced in rain-fed areas, while 13 percent irrigated their fields. Irrigation is most important in central Thailand, where 27 percent of sugar cane farmers irrigated their fields. In all other regions, the proportion of sugar cane farmers irrigating their fields is less than 3 percent.
Energy
The bagasse resulting from the production of sugar cane juice is dried and used as fuel (combined use).
Biodiversity/Air pollution
Burning down sugar cane fields serves to reduce the number of dangerous animals in the sugar cane for the harvesters and to facilitate harvesting/transport. Only the stalks are needed to produce sugar/sugar cane. This leads to the loss of biodiversity and air pollution (smog, dust). Harvesting by machine is more environmentally friendly but is done at the expense of jobs. On the other hand, jobs with higher qualifications and higher wages are created. In Thailand, many sugar cane fields are still being burned. Government programmes provide loans and grants to purchase harvesting machinery, thus reducing the proportion of such practices.
Total Corbion PLA
Corbion Purac uses sugar cane from Thailand for the production of lactic acid and lactides. Little information is available regarding the cultivation of sugar cane for Corbion Purac. The company purchases sugar from over ten mills. The majority of the sugar demand is covered in the region so that transport distances are as short as possible.
It should be noted that companies with cultivation certifications only supply certified goods when the customer explicitly requests it.
NatureWorks
NatureWorks is certified according to ISCC PLUS (International Sustainability and Carbon Certification) for its current site in Blair. The ordered quantity of GMO-free goods such as maize is produced but is processed together with GMO maize to produce the lactic acid required for PLA. However, an independent body (Eurofins GeneScan) guarantees through analyses that no GMOs are detectable in the PLA.
Total Corbion PLA
Most of the sugar is sourced from Thailand. Corbion is a member of Bonsucro and SEDEX and is certified by Bonsucro. For interested customers, Total Corbion supplies Bonsucro-certified PLA.
If maize from the USA is used for the production of PLA, it is highly likely to be GMO maize. Therefore, there must be a specific assessment by region and producer. GMO-free alternatives are increasingly available.
Total Corbion PLA
The producer offers a non-GM alternative to PLA with specific processing characteristics, where the lactic acid is produced from the raw material sugar cane. Prices are approximately 2 euros per kilogram for PLA similar to that from NatureWorks and approximately 2.50 euros per kilogram for heat-stable PLA. The raw material is grown in Thailand and processed in the country, in Rayong. The production capacity for PLA is approx. 75,000 tonnes per year.
The material recycling of PLA or its blends has not yet taken place on an industrial scale due to the small quantities available. Composting is currently prohibited in Germany under the Packaging Act and the Organic Waste Act. In agriculture and horticulture, bio-based and biodegradable mulch and cover films can offer economic advantages over non-degradable films.
Hence, the reason why it is categorised under “assessment in individual cases” (yellow) is the legal situation with regard to composting in Germany and the lack of a recycling system, rather than the end-of-life options offered by the manufacturers.
Recycling
In principle, PLA blends can be chemically or mechanically recycled, provided that sufficient quantities are available. Currently, PLA blends are sorted out, enter the mixed plastic fraction and are incinerated for energy generation. Depending on how state-of-the-art the plant is, sorting with infrared is technically possible for PLA blends, but requires additional investment.
In principle, biopolymer film materials, such as materials from PLA copolyester blends, can contaminate the existing recycling paths of typical film materials such as PE. Bioplastics in dimensionally stable bottle, thermoformed tray or cup applications such as PLA blends, on the other hand, would primarily have adverse effects on the PET and PS flows. In Germany, no beverage bottles made of PLA blends are currently in use. Therefore, there is practically no risk of contamination.
The question of what percentage of bio-based plastics can be added to conventional plastics without causing problems has resulted in a controversial discussion. It is assumed that contamination of PET caused by PLA blends is problematic even at much lower levels than contamination of PE. PLA blends with a density of more than 1 g/cm3 are sorted out as impurities or residual material, thus not entering the further recycling process and are therefore not relevant with regard to disruption to recycling. If PLA blends with a density of less than 1 g/cm³ were produced and entered into the recycling process, they would also impact the recycling process.
NatureWork states that Ingeo can be recycled, composted and fermented. Composting is possible if the following conditions are met: temperatures above 60 °C, 95% humidity and the presence of microorganisms. The material should be shredded and mixed with other material. Fermentation is expedient in thermophilic dry systems with high temperatures (production of methane).
Composting should be limited to only a few special cases. As a rule, energy recovery is more sensible since the energy contained in the plastic can then still be recovered. NatureWorks states that end products made 100% from Ingeo are compostable in municipal and industrial plants according to the following standards: DIN V 54900-1 (Germany), DIN EN 13432 (EU), ASTM 6400-04 (USA), GreenPla (Japan).
BASF
The company’s preferred option is composting, which is classified as “organic recycling” according to EU directives. Ecoflex® and ecovio® are certified according to DIN EN 13432, ASTM D6400, ISO 20200 and Vinçotte (“OK compost” and “OK compost HOME”).
In view of the currently limited volume of compostable plastics, the best alternative recovery method according to BASF is incineration if composting is not possible. Mechanical recycling of the production waste generated during production is possible and corresponds to the current state of the art.
Coveris
Coveris states that the raw materials used are certified according to DIN EN 13432. The co-extruded PLA blend is also compostable, i.e. it can be certified according to DIN EN 13432.
FKUR
The in-house recycling of production waste or rejects generated during production is possible if they are separated according to type. Depending on the application, up to 20 percent recyclate can be added to the new material. Many Bio-Flex® types are certified according to DIN EN 13432 and ASTM D6400 and are therefore considered compostable materials for industrial composting.
Taghleef
This company chemically recycles its own PLA production waste. Up to 50 percent of the recycled material can be added to the process when the PLA is dried at low temperatures and cooled to a maximum of 50 °C.
Cups/folding trays
According to ifeu’s assessment of the status quo, dimensionally stable packaging made of PLA has no overall ecological advantage, but no disadvantage either. All life cycle assessments refer to the production of Ingeo by NatureWorks in the US Midwest. The relatively high environmental pollution due to sulphur oxide, nitrogen oxide and particulate matter emissions comes from the high proportion of coal-fired power generation there.
The decisive life cycle stage in the acidification potential impact category for PLA production is lactic acid production. Above-average amounts are largely due to the sulphuric acid precursor chain. This process will have a significantly lower environmental impact in the future. The energy and process resource requirements should be significantly reduced and the process yield improved.
NatureWorks
NatureWorks prepares its life cycle assessments of PLA on the basis of primary data on resource and energy consumption and emissions, which the company collects every three to four years in the form of an “Eco-Profile“. Unlike other companies, NatureWorks also makes this data available online for download. NatureWorks has continuously improved in terms of its life cycle assessment since the start of production: Today it produces 60 percent less greenhouse gases and uses 50 percent less non-renewable energy than oil-based PET or PS, which is being replaced.
BASF
Life Cycle Assessments (LCA) exist for BASF’s PLA blends for carrier bags and mulch films.
Total Corbion PLA
In 2010, a cradle-to-gate LCA was published for the first time. It covers the cultivation, grinding of sugar cane, production of auxiliary chemicals, transport and production of lactides and PLAs. Here, you will find the current LCA, which also takes into account the process chain.
Taghleef
Taghleef has compiled an LCA with five categories for products produced at the Italian site. The following were included: Raw material production, processing, distribution, use and disposal, including all transport steps. In 2010, a “Quantification and Statement of Greenhouse Gas Emissions“ was compiled for the Italian site in accordance with ISO 14064-1:2006.
The material PLA has a very high bio-based content.
However, it is also increasingly frequently used in blends; in this case, the bio-based content of the blends is to be taken into account.
Specific values are available from the following companies:
NatureWorks (Ingeo): 99.7% bio-based content
Taghleef (Nativia): > 80% bio-based content
FKUR (Bio-FLEX®, compounds based on PLA): 10 to 90% bio-based content; current developments aim to increase the bio-based content of all products to at least 50%.
BASF (ecovio®, ecoflex®/PLA blend): approx. 10 to over 95% bio-based content
2. Social compatibility


For the social compatibility criterion, the assessment refers to the existence of social standards in cultivation and processing. These can be internationally valid guidelines, national legal standards or private sector standards. The social standards of the country from which the raw material originates or in which the processing takes place are used as a basis for the assessment.
The assessment must be specific to each production area and standard.
In addition to internationally valid standards, companies also have their own social standards.
NatureWorks
This company is certified according to ISCC PLUS (International Sustainability and Carbon Certification) for its current site in Blair. Certification is also being sought for the planned site in Thailand.
Total Corbion PLA
Most of the sugar for PLA production is sourced from Thailand. The parent company Corbion is a member of Bonsucro and SEDEX and is certified by Bonsucro. The suppliers (sugar cane mills) are encouraged to have themselves certified according to both standards.
Some of the larger suppliers are members of SEDEX, and some also supply sugar to larger brand name companies, e.g. the beverage industry, and have therefore established their own codes of conduct covering social and environmental aspects.
A code of conduct exists but is not certified by independent third parties.
BASF
BASF has developed its own system to analyse the three sustainability criteria of economy, environment and social aspects and to present them using the instrument SEEbalance®. By means of life cycle assessment, life cycle costing, social life cycle assessment and social hotspot assessment according to the UN SDGs (UN Sustainable Development Goals), the data is evaluated in an eco-efficiency analysis according to ISO 14045, ISO 14040/44 and social analysis. Sustainability activities are condensed in the overall view of SEEbalance®. The entire value chain of suppliers, transport, production and customers is taken into account.
Taghleef
This company has an Ethics Code for its Italian site.
Different standards and whether a company is independently certified must be taken into account in the assessment.
NatureWorks
NatureWorks produces in the USA. This means that American standards apply.
Total Corbion PLA
Total Corbion PLA produces lactic acid, lactide and PLA in Rayong (Thailand). The production is covered by the Bonsucro certification. The company has its own code of conduct.
BASF
BASF has developed its own system to analyse the three sustainability criteria of economy, environment and social aspects and to present them using the instrument SEEbalance®. By means of life cycle assessment, life cycle costing, social life cycle assessment and social hotspot assessment according to the UN SDGs (UN Sustainable Development Goals), the data is evaluated in an eco-efficiency analysis according to ISO 14045, ISO 14040/44 and social analysis. Sustainability activities are condensed in the overall view of SEEbalance®. The entire value chain of suppliers, transport, production and customers is taken into account.
FKUR
This company is certified according to the GKV Code of Conduct of the German Association of the Plastics Converters (GKV).
Taghleef
Taghleef is certified according to BS OHSAS 18001 and a member of SEDEX.
Wentus
This company is certified according to the GKV Code of Conduct.
3. Safety and technology


Product quality must be guaranteed. The packaging must not react with the product and must prevent it from reacting with the external environment. Regarding technology, the technological processability of the packaging material is evaluated. Can it be processed on standard machines? What adjustments, if any, must be made? Are there any compromises in terms of quality, processing speed or durability?
PLA consists almost exclusively of polylactic acid. Since PLA is very brittle without additives, various additives are added to the material, depending on the application. This makes it easier to process.
NatureWorks:
NatureWorks lists on its website – in this case for bottles – which types of additives are usually used. These mainly include stabilisers, colourants, UV blockers, nucleating agents and process aids. NatureWorks provides recommendations for suppliers of additives but also recommends the use of other suppliers.
In the process used by NatureWorks, the polylactide is polymerised from the dilactide using a catalyst.
The PLA from NatureWorks has been approved by the FDA. Concerning Regulation (EU) No 10/2011, NatureWorks informs that with regard to the migration, the manufacturer and user must check whether the specifications are met for the respective application.
Safety data sheets and further technical data are available for download on the website of the manufacturer NatureWorks.
Since PLA offers a wide range of possible applications, it is recommended to contact the manufacturer directly. Further sources of information in the form of data sheets can be obtained from Total Corbion PLA and Taghleef.
For films:
If additives are used to prevent fogging, the conformity of these additives must be checked, as they are surface-active.
For laminates with cellophanes, glycerol esters and metal salts which comply with FDA guidelines are used.
For containers:
For special product applications (headspace oxygen absorber for bottles, absorber for packaging with barrier layer) the addition of an oxygen absorber is conceivable.
Processing can be carried out on traditional processing machines (extrusion). The processing temperatures vary greatly depending on the PLA structure and are 100–180 °C. The sealing temperatures must be controlled accordingly. Thus, the ability to precisely control the temperature on the production line is an important mechanical requirement.
NatureWorks: Ingeo is a semi-crystalline polymer with very low crystallisation rates. Processing on crystallisation systems is generally not possible. As a result of the amorphous structure, decomposition occurs in the presence of water when the product is heated. For this reason, all products must be pre-dried very well. Often, the recycled product is crystallised before processing. The target is a water content of less than 250 ppm. The low resistance to ethyl acetate (EtAc), which is used in many printing processes, should also be noted. At 2% EtAc or greater, the layers may stick together. The manufacturer provides suggestions on suitable printing inks and packaging materials that can be used for lamination. Another problem is the low stability against isopropanol.
Corbion Purac: Two PLA variants are offered. (Amorphous) standard PLA with low heat stability is produced from a mixture of D and L lactic acid. Due to its amorphous structure, this material also decomposes when exposed to heat in the presence of water. In addition, there is a more heat-stable variant which is produced with D-lactic acid homopolymers using a special technology. According to the manufacturer, this material is stable up to temperatures of 180 °C. Pre-drying is also necessary here. For injection moulding, the processing temperatures are 90–100 °C. Here, you will find further information from the manufacturer. |
According to DIN 53122, the water vapour permeability of PLA is 20–80 g/m2d. There is also an oxygen permeability of 500–600 cm³/(m²*d*bar) and a carbon dioxide permeability of 2500–3500 cm³/(m²*d*bar). The desired material properties can be achieved by appropriate film finishing such as lamination.
Manufacturers as well as compounders provide corresponding data.
As PLA is already used in various applications, packaging manufacturers have practical experience with the respective applications. However, since these tests are often carried out in close cooperation with food manufacturers, this information is not always publicly available. In this case, it is advisable to work closely with the packaging manufacturer. A prerequisite for the production of application-oriented blends is the purchase of sufficient quantities.
4. Quality


The quality criterion encompasses the legal requirements for packaging material (section 4.1). According to the German Federal Institute for Risk Assessment (BfR) standards, “quality” means compliance with the legal requirements and BfR specifications for packaging. Ecological and environmental aspects are important criteria for bio-based packaging. Packaging reactions with different goods and thus different stability requirements must be avoided. At the same time, excessive demands can lead to costly, unsustainable packaging. Bio-based packaging often offers advantages such as longer shelf life or biodegradability. Consumers demand transparent and truly sustainable packaging with the same handling quality.
Where the use of PLA as a packaging material for foodstuffs is concerned, the legal requirements described in the general section apply. To date, there are no specific requirements for PLA. The manufacturer NatureWorks writes on its website that the product PLA is non-hazardous. However, the manufacturer of the additives should be contacted regarding the additives used to confirm that they are harmless.
Ideal conditions exist for the use of fresh vegetables and bakery products where high water vapour permeability is desired for short storage periods.
Lid applications
PLA offers good aroma protection at low temperatures. It has good barrier properties against fats and oils. NatureWorks provides detailed information regarding sealability and printability.
For this purpose, tests must be carried out in advance to achieve the desired result.
Shrink films or shrink tapes
If shrink films or shrink tapes are used, a lower temperature control is very important to achieve a satisfactory result. When replacing PVC shrink tapes with Ingeo products, please follow NatureWorks’ instructions.
PLA has very versatile application possibilities. An extensive collection of technical material data can be consulted in the biopolymer database of IfBB Hannover (Institute for Bioplastics and Biocomposites, Hannover University of Applied Sciences and Arts) and the company M-Base GmbH.
The consumer requirements regarding safe packaging are guaranteed with PLA. It should be noted, however, that the material is generally used for products with a best before date of less than six months.
Use for products with a longer best before date is possible in exceptional cases after intensive testing.
The product is relatively stiff and has a nice shine. Films with very high PLA content tend to rustle. More flexible blends like ecovio® do not rustle as much. The material has very good adhesive properties for labels.
Printing
Temperature control must be maintained when printing PLA films. Even hot zones that occur for very short periods (e.g. rollers) can lead to deformations such as shrinkage. However, there are also film types that are slightly more temperature-stable.
Surface treatments such as corona treatment or chemical treatments are used to improve ink adhesion. NatureWorks provides detailed information regarding sealability and printability. For this purpose, tests must be carried out in advance to achieve the desired result.
Lid applications
PLA can be used as a flat lid or as a film for sealing containers.
PLA does not tolerate increased storage temperatures (> 35 degrees) or direct sunlight. This applies to both the blanks and the processed end product. With regard to the mechanical strength of the packaging material, the manufacturer’s specifications must be observed.
With regard to stability, there are limitations for isopropanol and ethyl acetate. Therefore, very dry ambient conditions are an essential aspect for the storage of blanks.
As PLA is already used in various applications, packaging manufacturers have practical experience with the respective applications. However, since these tests are often carried out in close cooperation with food manufacturers, this information is not always publicly available.
In this case, it is advisable to work closely with the packaging manufacturer. A prerequisite for the production of application-oriented blends is the purchase of sufficient quantities.