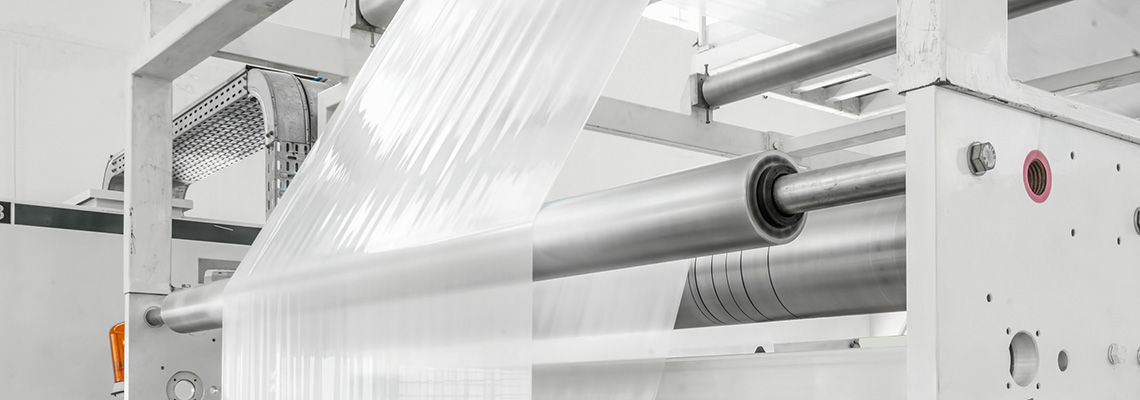
Polyethylene made from biomass (bio-PE) is produced in Brazil from GMO-free sugar cane. The only significant producer of the material is the company Braskem with a production capacity of approximately 200,000 tonnes annually. Currently, about 30 variants of the types HDPE, LLDPE and LDPE are produced.
Biomass-based PE is what is called a “drop-in” solution, as it has the same chemical structure as mineral oil-based PE. The latter can thus be replaced one-to-one with bio-PE – both in terms of applications and disposal.
Recyclability and prices
Products made of bio-PE are 100 percent recyclable. Recycling produces recyclates, i.e. reusable plastics. Their use in food packaging is currently not permitted legally. Therefore, PE is downcycled via cascade use. Bio-PE is ecologically more advantageous if it remains in the recycling system and the carbon from the sugar cane remains bound in the PE. As such, bio-PE is considered a product with a negative carbon footprint.
No reliable statement can be made about the future price development of biomass-based PE. Important influencing factors include raw material prices (sugar, ethanol), currency price differences, the competitive situation with conventional PE or possibly with other suppliers of biomass-based PE and the development of demand. Due to its status as a drop-in solution, the prices of biomass-based PE will be based on the price of PE, a comparatively inexpensive mass plastic.
PE is resistant to almost all polar solvents, acids, alkalis, water and alcohol. It has a good temperature resistance and can be processed in a wide temperature range. The properties of the plastics can be consulted in the CAMPUS materials database.
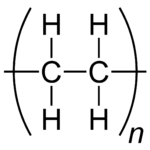
Kontakt
Braskem is the largest polymer producer in South and North America. It produces both biomass-based PE and conventional PE. The brand name for its bio-PE is “I’m greenTM” and is referred to in the following as “Green-PE” or generally as bio-PE. The bioethanol required for this is produced from sugar cane. At the Triunfo Petrochemical Complex production site in Rio Grande do Sul (RS) in the south of Brazil, ethanol produced from sugar cane is dehydrated and thus converted into ethylene (a precursor product to bio-PE). The production capacity is 200,000 tonnes per year.
The bio-ethylene produced is used by plastics converters to extrude the PE films. In addition to those listed here, there are numerous other plastics converters.
Coveris
Coveris is the sixth-largest manufacturer of packaging solutions in the world, with subsidiaries in 21 countries and sales of 2.5 billion US dollars. It extrudes PE films and laminates them in different variants: bio-based composite films with PET-O, PP-O, PA-O and NatureFlex™ cellophane films for tubular bag applications in the food and non-food sectors. The processing locations in Germany are Warburg and Halle/Westphalia.
FKuR Kunststoff GmbH
FKuR is a bioplastics specialist with a broad portfolio of granules made of compostable/biodegradable and bio-based plastics. These can be raw materials as well as plastic blends. The company’s headquarters and production site are located in Willich, in the Lower Rhine region. As the European distribution partner of the Brazilian company Braskem, FKuR sells the bio-based PE. FKuR also offers other product lines of bio-based/biodegradable packaging plastics such as Bio-Flex®, Biograde®, Fibrolon® and Terralene®. In addition to the packaging materials it produces, FKuR sells bio-based raw materials from various manufacturers (biomass-based PE from Braskem, biomass-based PET from Toyota Tsusho, bio-PA from Evonik). Further information on the products and their processing can be found on the website.
Inzea Biopolymeres
Inzea produces 40% bio-based, large PE bags up to 25 kg and octabins, i.e. octagonal containers.
For further information, click here.
Tetra Pak GmbH & CO KG
Tetra Pak describes itself as a total solutions provider for food packaging. The Tetra Rex ® series uses bio-based PE. The beverage cartons feature a 100% bio-based PE layer on the outside and inside. In addition, its closures are made of bio-PE. The switch is also planned for other models.
PE is the most frequently used packaging material for food packaging – due to its favourable price combined with a comprehensive performance profile.
It is important to note that special pre-treatments are required for gluing and printing, while sealing is generally straightforward. The materials used for films such as packaging films, shrink films and bags are usually made of the polymer variants LDPE (branched low-density polyethylene) and LLDPE (linear low-density polyethylene). HDPE (linear high-density polyethylene) is used to produce hollow bodies such as bottles and containers using the blow moulding process, and it is also possible to shape trays and cups by thermoforming.
One very important source of data for the material properties of biopolymers and the packaging materials produced from them is the biopolymer database of IfBB Hannover (Institute for Bioplastics and Biocomposites, Hannover University of Applied Sciences and Arts) and the company M-Base GmbH.
films/bags: all types of film packaging, e.g. bags for frozen products, shrink films, stretch films
cups: all types of container packaging, trays, cosmetics
bottles: Cosmetics, beverages, detergents, chemicals
Other applications: coating of paper packaging, caps, canisters, tubes
PE is resistant to almost all polar solvents, acids, alkalis, water and alcohol. It has a good temperature resistance and can be processed in a wide temperature range. The properties of various PE types can be consulted in the CAMPUS® materials database for plastics.
The biopolymer database lists the material properties of PE variants in detail according to use. Different variants of HDPE, LLDPE and LDPE are produced for a wide range of applications.
Various processes can be used to produce bio-based PE. The choice of raw material is influenced by the process and the region. In general, the price of the raw material (based on the tonnage of usable carbon) also plays an important role.
For ethanol-based processes, a wide variety of sugar sources such as sugar cane, barley, cassava, wheat, potatoes, sugar beet and sago can be used. More expensive, but also already possible, is the use of non-food sugar sources such as wood or agricultural waste (straw). These alternative sources of bioethanol (advanced bioethanol, second-generation ethanol) are already available today. Other processes can also use vegetable oils or food waste. However, they are not yet industrially established. DOW is collaborating with various manufacturers on the implementation of production. Depending on the process and PE variant, there are also differences in the bio-based content of the PE. According to Braskem, the bio-based content is between 80–100% depending on the product. The choice of raw materials also significantly determines the amount of land required.
Sustainability criteria

1. Ecology


For the ecology criterion, seven sub-criteria (parameters), which are considered essential for organic food production, have been included in the assessment: land use/competition for food, environmental compatibility, certifications (cultivation and processing), genetic engineering, disposal (recycling, composting), life cycle assessments and bio-based content.
After Colombia, Brazil has the most efficient and productive sugar and bioethanol production infrastructure in the world with by far the highest production volume.
Braskem states that an area of approx. 68,000 hectares or 0.02 percent of Brazil’s available arable land is required to produce 200,000 tonnes of biomass-based PE from sugar cane and bioethanol. This corresponds to three tonnes of PE per hectare. According to the Institute for Bioplastics and Biocomposites (IfBB), 0.46 hectares or 33.55 tonnes of sugar cane are required for one tonne of 100% PE.
Only sugar cane is used for the production of biomass-based PE. 39 percent of Brazil’s total area can be used for agriculture, 58 percent is protected or natural habitats. Today, 2.4 percent of Brazil’s arable land is used for the cultivation of sugar cane. About half of the sugar contained in the plant is used for food, while the other half is used for bioethanol production (installed process combination with a certain degree of flexibility). There are currently 441 sugar cane mills, of which 61 percent produce ethanol.
Cultivation of sugar cane
Sugar cane is a perennial plant with stems up to seven metres high and five centimetres thick and sugar-storing pith (7–20 percent sucrose). It has high requirements where heat (optimum: 25 to 28 degrees), water (optimum: 1,200 to 1,500 mm of precipitation) and nutrients are concerned, and is often grown as a monoculture for perennial use (2 to 10 years). Depending on the location, variety and cultivation conditions, the plants require 80 to 200 kilograms of nitrogen per hectare and up to 350 kilograms of potassium per hectare. The use of synthetic fertilisers is reduced via the use of by-products. Phosphate fertilisation is of less importance. Sugar cane has a fungal flora that increases the absorption of phosphate. Sugar cane is harvested by hand or by machine. However, the proportion of manual labour will decrease in the future (cf. section on “Biodiversity/Air pollution”).
Sugar cane is a robust crop, generally grown on the same land for five consecutive years.
Water consumption
In Brazil, sugar cane is grown mainly in the central-southern part of the country, where the high rainfall almost always allows it to be grown without irrigation. Water is mainly consumed in the processing of sugar cane. A considerable amount is needed for cleaning the raw product.
Energy consumption
In general, ethanol production requires a lot of energy. However, the use of heat and electricity generated during the production process by burning bagasse (co-product of the grinding process in ethanol production) covers a large portion of the energy needs. Most of the sugar cane mills are therefore self-sufficient in terms of energy. Furthermore, the bagasse is used as an energy source for electricity generation. Surplus electricity is fed into the local power grid.
Biodiversity/Air pollution
The burning of sugar cane fields is harmful to the atmosphere and biodiversity. It makes harvesting easier by removing the sharp leaves from the stalks and protecting workers from dangerous animals. Harvesting by machine without burning is more environmentally friendly but is detrimental to jobs.
Under an agreement between the sugar cane producers and the government of the state of São Paulo, the burning of fields has been banned here since 2017, while it has not yet been banned in other parts of the country or in other countries.
Cultivation of sugar cane in Brazil
The main sugar cane growing area is the State of São Paulo. Brazil has a strict regime regarding the regulation of sugar cane cultivation and nature conservation. Several laws have been enacted to control the cultivation of sugar cane. The rules established by Agro-Ecological Zoning apply nationwide. These laws are not always observed, and land is still classified as “degraded” because it can then be used for agricultural purposes. Braskem follows stricter rules.
Environmental management
Braskem is involved in the “Responsible Care Program“. This voluntary initiative of the global chemical industry aims to improve the environmental management of chemical companies and their supply chain. The criteria are occupational safety, processes and products, maintaining the health of workers, and protecting the environment.
It should be noted that companies with cultivation certifications only supply certified goods when the customer explicitly requests it. Here is an overview of Braskem’s certifications.
Braskem is member of Bonsucro and ISCC PLUS certified. ISCC certified goods are available in any quantity upon request (chain of custody product chain certification). Bonsucro-certified ethanol is also available. It should be noted that Bonsucro, unlike ISCC PLUS, does not yet have a chain of custody certification for the products downstream of the ethanol. In both systems, the costs for the certification have to be borne by the customer. ISO 14001 certifications are available for most sites. Certification by TÜV Austria (formerly Vinçotte) confirms that the bio-based content of Braskem’s Green PE is over 80 percent.
Bio-based PE has the same recycling properties (drop-in solution) as conventional PE and can therefore be recycled together with it without any problems.
However, it should be noted that, although the PE recycling system is well developed in itself, many PE films are not recycled, but instead used for thermal recycling (incineration). This applies especially to films < 2 x 2 cm. Depending on the sorting system, the separation size is between 5–100 cm². Incineration of biomass-based PE is possible. It is stable when disposed of in a landfill and is not biodegradable.
At the manufacturer Coveris, film/production waste is regranulated and reused wherever possible.
A comparative analysis of the environmental impact of films made of biomass-based PE and fossil PE (PE-LD) was carried out by ifeu (Institut für Energie- und Umweltforschung Heidelberg GmbH) on behalf of the German Environment Agency. According to this study, film packaging made of biomass-based PE has a lower environmental impact in terms of the indicators of climate change, fossil resource consumption and summer smog. In contrast, a higher environmental impact was identified for acidification potential, terrestrial and aquatic eutrophication and human toxicity (particulate matter).
The life cycle of “Green PE”
At the beginning of 2014, the abridged version of a cradle-to-gate life cycle assessment (LCA) certified according to ISO 14040/ISO 14044 was published. The full LCA study report is not publicly available. The analysis is based on data from three mills (which together represent 62 percent of Braskem’s suppliers) and the average of the sugar cane mills that supply Braskem in the Centre-South region.
According to Braskem, the LCA shows that sugar cane cultivation enriches the soil with carbon (in a calculated scenario). Green PE would receive emission credits of about one tonne of CO2 equivalents. However, the LCA does not show this directly but uses figures from a separate study on land use. Hence, the figures should be used more defensively.
The following impact categories were evaluated in total: greenhouse gas potential, fossil resource use, eutrophication, acidification, ozone depletion, photochemical ozone creation potential. Biomass-based PE scores positively on greenhouse gas formation (negative 2.15 tonnes compared to positive 1.83 tonnes for fossil PE from Braskem). Green PE also performs better in terms of fossil resource consumption, as more than 80 percent of the energy used for production comes from renewable sources.
In the impact categories eutrophication and acidification, fossil PE fares better. Eutrophication can be attributed to sugar cane cultivation and the associated phosphate and phosphorus emissions. The acidification values result from bagasse combustion, fuel consumption for agricultural vehicles and the burning of fields before harvest (note from the editorial team: this practice has ceased since 2018). The ozone parameters are similar for both materials, with a slightly higher value for Green PE.
To supplement the LCA, Braskem commissioned two further studies: an assessment of land use changes and a water footprint.
The results can be seen in this presentation. It should be noted, however, that the assessments and conclusions were formulated by Braskem itself.
Bio-based PE has a very high percentage of bio-based material. However, it is also increasingly frequently used in material composites; in this case, the bio-based content of the total material composite is to be taken into account.
Specific values are available from the following companies:
Braskem
Braskem is certified by TÜV Austria (formerly Vinçotte) with 4 stars, i.e. the bio-based content of Green PE is at least 80 percent, but typically > 90 percent. According to Braskem, each class of biomass-based PE has a different bio-based content due to the different formulations. HDPE has a content of at least 96 percent, while LLDPE has a content of at least 84 percent. This is due to the higher proportion of fossil comonomers, e.g. butene and hexene.
According to the American standard ASTM D 6866 and/or ISO 16620, Parts 1–3, the bio-based carbon content can be determined and certified analytically and by calculation.
Coveris
Coveris aims to achieve a bio-based content of at least approx. 35 percent according to ASTM D6866 for all films made using biomass-based PE and achieves values of up to 85 percent.
FKuR
According to FKuR, the beverage crates distributed by two manufacturers have a bio-based content of approximately 62 percent. The manufacturers are Schöller Alibert and Oberland; the granulate comes from FKuR (Terralene®).
2. Social compatibility

For the social compatibility criterion, the assessment refers to the existence of social standards in cultivation and processing. These can be internationally valid guidelines, national legal standards or private sector standards. The social standards of the country from which the raw material originates or in which the processing takes place are used as a basis for the assessment.
Brazil’s sugar and ethanol industry employs about 800,000 people. The introduction of modern agricultural practices has had a major impact on workers, as laws have been established to combat child labour and working conditions similar to slavery.
In 2009, the government, industrial companies and trade unions signed the “National Commitment to Improve Labor Conditions on Sugarcane Plantations”. It lists 30 measures which aim to protect the dignity and rights of workers and regulate working conditions in the industry. For example, it specifies that workers are to be recruited without intermediaries, makes compensation payments more transparent, supports temporary migrant workers, improves health and safety at work and the transportation of food, and promotes trade unions and collective bargaining activities.
There is also the São Paulo State Agro-environmental Protocol for the ethanol/sugar industry (also known as the Green Protocol), which was signed by UNICA (the Brazilian Sugarcane Industry Association), ORPLANA (Organization of Sugarcane Growers of the Center-South region) and the Government of the State of São Paulo in 2007. The topics it addresses include the conservation of soil and water areas, forest protection, the recovery of riparian forests, the minimisation of climate-impacting gases and the minimisation of the use of agrochemicals and fertilisers. The main objective was to stop the burning of sugar cane fields. This practice has now ceased.
There are also industry programmes that support technical training programmes for workers, such as the “Program to Re-qualify Sugarcane Workers (RenovAção)”, which (re-)trains 6,000 workers and community members each year. The target group is mainly sugar cane cutters who lose their jobs because the planting and harvesting processes are mechanised.
Braskem’s code of conduct
Braskem has developed its own Code of Conduct for its ethanol suppliers (together with ProForest, an independent consultancy firm), based on but also going beyond Brazilian (regional and national) legislation.
This code includes both social and environmental requirements with which ethanol suppliers (sugar cane mills) must comply if they wish to supply Braskem. Since 2012/2013, an independent audit (auditor: Control Union) checks compliance with the requirements every two years. Suppliers must provide an action plan for improvements. So far, at least 90 percent of the suppliers are audited, which corresponds to 80 percent of the supplied ethanol.
In addition, the company started a 3-year programme called “Solidaridad” in 2014 with the aim of gaining more knowledge about the supply chain. Besides Braskem itself, a cooperative of sugar cane producers, sugar cane mills and customers are participating.
Braskem is also Bonsucro certified (see section “1.3 Certifications”).
The following certifications are in use: SEDEX, GKV Code of Conduct and OHSAS 18001.
SEDEX – Management tool for suppliers
Sedex is a non-profit organisation that promotes responsible and ethical business practices in global supply chains. Its main service is an online database that allows members to store, share and report information on four key areas (labour standards, health and safety, environmental ethics and business ethics). Users can evaluate and compare the efforts of their suppliers with the requirements of recognised standards, such as ILO standards, ETI Base Code, SA8000, ISO14001 and industry-specific codes of conduct. A proprietary standard does not exist.
GKV Code of Conduct
This Code of Conduct is sponsored by the German Association of the Plastics Converters (GKV). It deals with obligations in the areas of environmental protection, health and employment protection, child labour, forced labour, human rights, wages and working hours.
OHSAS 18001 – Occupational Health & Safety Advisory Services (occupational health and safety management system)
BS OHSAS 18001 will be replaced by DIN ISO 45001:2018 in a 3-year transition phase. It is a British standard that is closely based on ISO 9001 (quality) and ISO 14001 (environment) and defines requirements for professional occupational health and safety management.
Social standards at Braskem
The company is a signatory to the UN Global Compact, a strategic initiative of the United Nations for companies that commit to aligning their business activities and strategies with ten universally recognised principles in the areas of human rights, labour standards, environmental protection and anti-corruption. Braskem is also involved in the Responsible Care Program – a voluntary initiative of the global chemical industry which aims to improve the environmental management of chemical companies and their supply chains. The criteria are occupational safety, processes and products, maintaining the health of workers, and protecting the environment.
Social standards at Coveris and FKuR
Coveris and FKuR produce in Germany; therefore, German/European social standards apply.
3. S
afety and technology
With the safety criterion, the focus is on safety for the consumer. Here, it is mainly migration potential which is considered. Regarding technology, the technological processability of the packaging material is evaluated.
Highly extensive data is available for biomass-based packaging materials made of the same material, such as bio-PE, as these have the same properties as traditional plastics.
Biomass-based PE has a comparable chemical composition to mineral oil-based PE; therefore, its material properties are known.
PE is a thermoplastic material to which additives (UV stabiliser, coupler, dispersing agent) are added during processing, depending on the application. Compared to other thermoplastics, it has good expansion characteristics, high cold impact resistance, good sliding friction behaviour and electrical insulation properties, as well as lower strength, hardness and rigidity. For pasteurisation or hot filling, the low softening temperature must be taken into account. There is very extensive information material on PE, e.g. in the Material Data Center.
PE is a very inexpensive mass product which is physiologically non-hazardous and practically odourless and tasteless. That is why it is widely used in the food industry.
However, its barrier properties are a critical aspect to take into account. These can be improved with EVOH or with coatings.
PE, which is risk-free in terms of migration, is processed by numerous compounders. With regard to the conditions of use, it is recommended to contact the manufacturer directly to obtain an assessment for the corresponding application.
For films
If additives are used to prevent fogging, the conformity of these additives must be checked, as they are surface-active. The additives can be added as a masterbatch or applied as a surface coating. During processing, the static charge of the films must be taken into account and reduced via mechanical precautions.
Good results have been achieved with water-based coatings. For laminates with cellophanes, glycerol esters and metal salts which comply with FDA guidelines are used.
Processing can be carried out on the traditional processing machines for fossil-based PE. However, the prerequisite is that the processing temperatures do not exceed 100 degrees. The sealing temperature is 85 degrees. Therefore, an important mechanical prerequisite is that the temperature of the machines can be controlled very precisely.
Compared to other mineral oil-based plastics, PE has lower barrier properties and does not offer sufficient migration protection in all cases. In non-critical applications, however, the barrier properties against acids, alkalis, moisture and gases are sufficient, which is why it is used on a large scale.
PE is offered in a very wide range of blends and is therefore suitable for a wide variety of applications. In order to minimise material expenditure and costs, it should be precisely defined which requirements the material must fulfil for the planned application.
4. Quality

The quality criterion encompasses the legal requirements for packaging material (section 4.1).
According to the German Federal Institute for Risk Assessment (BfR), “quality” means compliance with the legal requirements and BfR specifications for packaging. Ecological and environmental aspects are important criteria for bio-based packaging. The packaged product results in specifications which the packaging material needs to fulfil and which should be precisely defined in advance. In many cases, excessive requirements lead to elaborate, expensive and unsustainable packaging. Consumers also demand transparent and sustainable packaging with the same usage properties. Due to the identical composition of the packaging material, bio-PE can replace mineral oil-based PE packaging solutions in many cases. However, specific requirements should be clarified by the company in advance.
Conditions of use of a packaging
At smaller manufacturers, different product ranges are to be packaged on the same packaging machine. Due to the identical composition of the packaging material, bio-PE can replace mineral oil-based PE packaging solutions in many cases. However, specific requirements should be clarified by the company in advance.
For the material polyethylene, the legal requirements are defined in the “Regulation on plastic materials and articles intended to come into contact with food” (regulation (EU) No 10/2011).
In the database “BfR Recommendations on Food Contact Materials“, the recommendations for PE are summarised under the serial number 030.
According to the current state of the art, the migration potential of PE is low. It is highest for LDPE with a low density of 0.88–0.90g/cm³.
If the use of a rather unusual ingredient or an unusual application is planned, an individual risk assessment should be performed.
Ideal conditions exist for the use of low-cost PE for products that do not have to meet specific requirements. However, it must be ensured that temperatures above 85 degrees do not occur over a long period of time during processing.
PE is a very light and versatile packaging material with medium barrier properties. It is particularly advantageous that PE is extremely odourless and therefore negative effects on the food are minimal, provided that no adhesives or printing inks with a strong odour are used. With regard to aromas and mineral oil hydrocarbons, PE does not provide a long-term and sufficient barrier. Protective gassing is not feasible without a coating.
The consumer requirements for a safe packaging material must be guaranteed. The stability of the bio-based packaging material is good; the packaging is easy to open and can be designed to be resealable. Consumers also generally expect as little packaging material as possible to be used.
In public perception, non-biodegradable plastics such as PE, which accumulate in the environment, are viewed very negatively – especially with regard to microplastics. On the other hand, the already existing recycling possibilities are a positive aspect.
The packaging material is relatively soft. If printing or gluing is to be performed, plasma treatment must be carried out beforehand.
In order to avoid misunderstandings among consumers, it should be communicated transparently how high the actual bio-based content in the end product is and what ecological advantages and disadvantages are associated with the raw material and/or the product.
Bio-based PE is just as stable as mineral oil-based PE. An additional coating can be applied to increase UV stability. PE can be stored for a very long time.
Highly extensive knowledge exists regarding different applications for polyethylene. The PE material for the respective application conditions can be chemically modified in many ways.
Further information on IK (Industrievereiningung Kunststoffverpackungen [Industry Association for Plastic Packaging]) and DVI (Deutsches Verpackungsinstitut [German Packaging Institute]) can be found here.