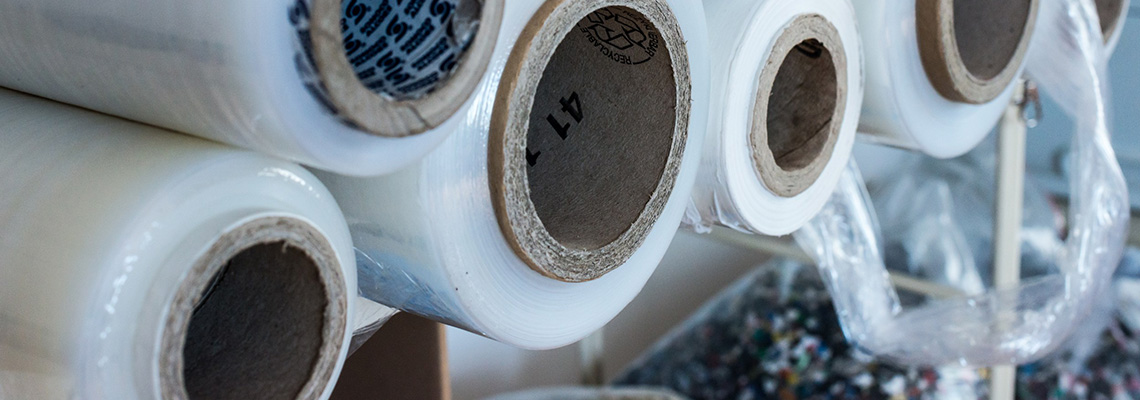
Cellulose is the most common natural polymer and is mainly derived from wood. With four billion hectares of forest, global wood growth is 5×1010 tonnes annually. Therefore, cellulose is an abundant source for the production of bioplastics which does not compete with food production. However, land use efficiency is lower compared to other bioplastics but still amounts to about 3 t/ha.
Cellulose is produced by plants as a semi-rigid skeletal substance, such that it cannot be processed like a thermoplastic material without modification. However, the possible applications are extremely broad thanks to chemical modifications.
It is the esters and ethers of cellulose which are mainly used, e.g. for coatings, cigarette filters, textile fibres, LCD displays and membranes, but also for packaging. They are often water-soluble and are processed into films, fibres or coatings by direct or indirect derivatisation.
Cellulose esters are a maximum of 50–60% bio-based since technical acetic acid and considerable amounts (up to 25%) of plasticisers – which are mostly petrochemical-based – are used in their production. Plasticisers such as triacetin (glycerol triacetate, partially bio-based), which are approved for use in the food sector, are used for packaging. Upon esterification, cellulose acetate (CA), cellulose butyrate (CB) or cellulose acetate butyrate (CAB) is produced after appropriate treatment, which can be processed thermoplastically. In the case of regenerated cellulose, substances such as NMMO (N-methylmorpholine-N-oxide) are used as a solvent during processing in a cycle. 99.5–99.7% of the solvent is recovered. This process is used to produce “Lyocell fibre” (e.g. for fruit and vegetable nets) by Lenzing. The process is more environmentally friendly than the viscose process and has better life cycle assessment values than cotton in many categories.
The films can be coated and laminated in a variety of ways to improve the sealing and barrier properties. Cellulose acetate is currently produced with technical acetic acid for economic reasons, but this could be replaced by bio-based acetic acid to produce a product with a higher proportion of renewable raw materials. Research is being conducted with the aim of reducing or avoiding the use of plasticisers.
The following is a non-exhaustive alphabetical list of the materials manufacturers and converters considered essential by the project team.
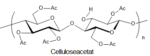
Symbol legend
positive evaluation
Evaluation in individual cases
predominantly critical evaluation
Kontakt
More than 95% of the world’s cellulose production is produced by the sulphate process (kraft process). In this process, the cellulose is broken down with sodium sulphide and sodium hydroxide. In larger pulp mills, recovery plants are connected to minimise the environmental impact.
Worldwide production volumes for pulp are estimated at over 130 million tonnes. Most of this goes to the paper and cardboard industry. About 50% of the world’s timber harvest is used for pulp processing.
Pulp mills, for example, are organised in the Arbeitsgemeinschaft der Rohholzverarbeiter (Association of Raw Wood Processors).
Zellstoff Stendal GmbH is a group of companies with large and modern processing plants.
Futamura Chemical Co.Ltd. (also known as Futamura)
Futamura processes pulp into film products and offers a very extensive range of cellulose products. Its annual capacity is 40,000 tonnes. Cellophane®, NatureFlex™ and Pearl™ are cellulose materials with different processing properties produced by Futamura using the viscose process.
NatureFlex™ is a flexible cellulose film made from renewable pulp with certified compostability (home and industrial composting) and very good barrier properties.
The cellulose is obtained in the “closed loop system”. In the process, chemicals are recovered.
Areas of application include labels and films, e.g. for dried food, confectionery, beverages, biscuits and baked goods, fresh products and takeaway food. The strong aroma barrier is ideal for the packaging of tea, coffee and cosmetic products.
The processing locations are Japan, Wigton (UK) and the USA. The raw material consists of cellulose, which is mainly produced from eucalyptus. The pulp comes from Europe, South America, North America, South Africa and Canada.
Celanese
Clarifoil® is a 100% subsidiary of the Celanese Group. Clarifoil is the world’s largest producer of cellulose diacetate films. It offers applications in the field of cardboard lamination. Information on applications as well as data sheets of the products manufactured can be found on the company’s website.
Daicel Polymer Ltd.
Daicel is a Japanese company with several production sites in Japan and Europe (Germany, Poland, France). In Germany, TOPAS Advanced Polymers handles the production. It produces cellulose acetates and hydroxyethyl cellulose for use in the food industry as adhesives. The website contains general information and data.
Eastman Chemical Company
The company produces chemicals, fibres and plastics and is a major supplier of cellulose acetate fibres. It produces various cellulose-containing plastics. The data sheets for the products sold are clearly shown in the “Products” section.
FKuR is a bioplastics specialist with a broad portfolio of compostable/biodegradable and bio-based plastics (raw material, plastic granulate). The company’s headquarters and production site are located in Germany. Under the brand name Biograde®, FKuR offers plastic compounds made from cellulose derivatives. For example, it produces bioplastics cutlery. Other product lines (Bio-Flex®, Fibrolon®, Terralene®) are offered for various applications. In addition to its own raw materials, FKuR sells bio-based raw materials from various manufacturers (bio-PE from Braskem, bio-PET from Toyota Tsusho, bio-PA from Evonik). Further information on the products and their processing can be found on the company’s website.
Under the PACKNATUR brand, fruit and vegetable nets made of regenerated cellulose are produced in this packaging centre. This cellulose packaging from the Austrian company is 100% biodegradable. The required wood is obtained in Austria.
NaturePlast is a supplier of various bio-based plastics, including cellulose derivatives. A consultation is offered for applications.
Klotz Verpackungen offers bags, films and folding boxes and operates an online shop.
The “Wentus” plastic from Clondalkin is primarily processed into a compostable waste bag. However, films made from cellulose and Mater-Bi® (Novamont) are also produced for packaging, e.g. for coffee. On request, the company will provide relevant documentation.
Application methods and material properties are listed on the manufacturers’ websites. One other very important source of data for the material properties of biopolymers and the packaging materials produced from them is the biopolymer database of IfBB Hannover (Institute for Bioplastics and Biocomposites, Hannover University of Applied Sciences and Arts).
Foils/bags: Cellulose hydrate, which is made from regenerated cellulose, is called cellophane or cell glass. This film is permeable to water vapour. With coatings, however, a good water vapour, gas and aroma barrier can be achieved. Packaging with controlled permeability for bakery products and in the fresh food sector by means of coatings is also possible. Very different material properties allow a wide range of applications from fresh vegetables to dried spices, tea or coffee.
Cups, thermoforming applications: These applications are still under development.
Bottles: So far, there are no applications, except for WPC.
Other applications: Textile fibres, ropes, additives, adhesives, cellulose acetate: e.g. cigarette filters, envelopes, brushes, cosmetic packaging
Films/bags: all types of film packaging, e.g. bags for frozen products, shrink films, stretch films, inexpensive mass products without special requirements
cups: all types of container packaging, trays, cosmetics
bottles: Cosmetics, beverages, detergents and cleaning agents, chemicals, surfactants
Other applications: coating of paper packaging, caps, canisters, tubes
Cellulose is a highly tear-resistant material with greatly varying properties – due to the different coatings and laminations. It can be given high barrier properties against aromas and oxygen, the mineral oil components MOSH/MOAH, or water. In addition, it can be specially equipped with specific barrier properties, such as higher water vapour permeability (with simultaneous barrier for microorganisms). It is heat stable up to 200 °C for 30 minutes.
Pulp, which is mainly obtained from wood, is the raw material for cellulose fibres. Considerable quantities (> 50 percent) of technical acetic acid or acetic anhydride are required for the production of cellulose acetate.
Wood is obtained from many regions and mainly from plantation cultivation. There are also large cultivation areas in Northern Europe which partly cover the demand for wood in Europe. Over 20 million tonnes were processed in Germany, of which over 55 percent were sold domestically. Over 80 percent of the raw materials used for this purpose come from waste paper.
Sustainability criteria
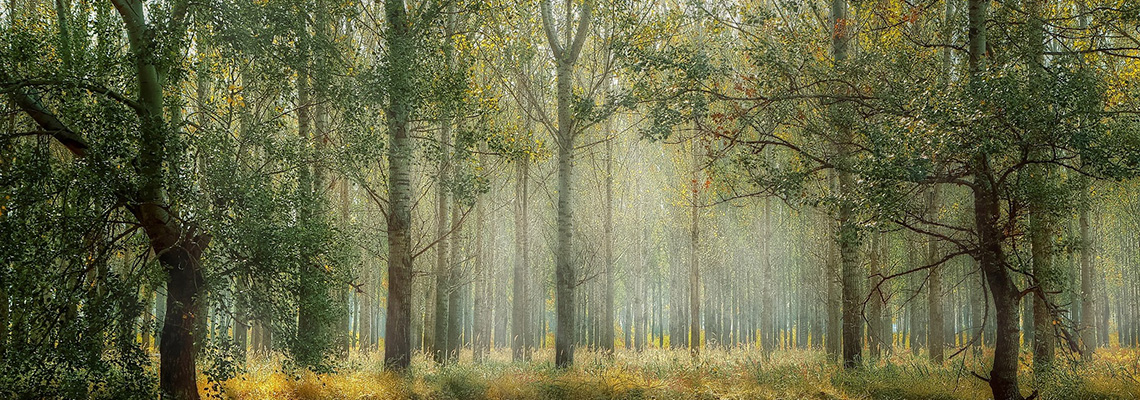
1. Ecology


For the ecology criterion, seven sub-criteria (parameters), which are considered essential for organic food production, have been included in the assessment: land use/competition for food, environmental compatibility, certifications (cultivation and processing), genetic engineering, disposal (recycling, composting), life cycle assessments and bio-based content.
The production of one tonne of cellulose diacetate, at a land consumption of 0.82 hectares, has a much better land efficiency than the production of one tonne of regenerated cellulose at 1.52 hectares.
Both materials come from the raw material wood and serve similar applications.
Processing routes for the production of the raw material wood
1.52 hectares (equivalent to 2.5 tonnes of timber) → Output: 1 tonne of regenerated cellulose
0.82 hectares (equivalent to 1.33 tonnes of timber) → Output: 1 tonne of cellulose diacetate
These values can vary greatly from region to region. It should be noted that the bio-based content can fluctuate considerably if multilayer films or coatings are involved. In this case, the bio-based content is sometimes well below 100 percent.
Eucalyptus trees are frequently used as the raw material for the production of cellulose worldwide.
Cultivation of eucalyptus
Eucalyptus is a heat-loving, frost-sensitive plant with a high water requirement. Its leaves contain essential oils and are therefore highly flammable. The trees have contributed to the development of forest fires in Australia and the US state of California.
Only a few of several hundred eucalyptus species are cultivated on plantations on a large scale worldwide. For pulp production, the trees are harvested after only seven years.
Basically, the production of regenerated cellulose is more complicated than the production of cellulose acetates and more chemicals are needed.
In the upstream process of pulp production, significant improvements have been achieved over the years, resulting in a significant reduction in water consumption and pollution from wastewater.
Production at Futamura
Futamura states that the raw material (i.e. pulp) is sourced from forests in Europe, South America, North America, South Africa and Canada. It is mainly eucalyptus that is used. The company operates according to the “Environmental policy” and the “Wood Pulp Sourcing Policy”.
Production at Clarifoil–Celanese
Information on Celanese’s sustainability efforts can be found here.
It should be noted that companies with cultivation certifications sometimes only supply certified goods when the customer explicitly requests it.
Futamura
The company Futamura is certified according to the following systems: FSC, PEFC, Chain of Custody und ISO 14001. Since the end of 2015, only certified pulp (FSC or PEFC) is used. Futamura obtains the raw material from forests in Europe, South America, North America, South Africa and Canada. It is mainly eucalyptus that is used.
Clarifoil
Clarifoil states that its film is made from pulp. The pulp comes from SFI-certified plantations and is 100% GMO free. The company is ISO 14001 certified.
Eucalyptus trees are frequently used as the raw material for the production of cellulose. This also applies for paper and cardboard packaging. GMO varieties have been authorised for eucalyptus trees in Brazil since 2015. Cultivation is expected to start in 2019/20.
Futamura
The company produces GMO-free packaging. No single component of the packaging may have been produced using or have been involved with GMOs.
Clarifoil
This company’s pulp also comes from SFI-certified plantations and is 100 percent GMO free.
When purchasing, it is important to ensure that the goods are FSC or PEFC certified.
While there are recycling systems for pulp products (paper, cardboard, paperboard), these are not yet established for cellulose-based bioplastics. Manufacturers mostly recycle waste from their own production.
Composting is recommended by the manufacturers but is currently not permitted by law in Germany. Hence, the reason why it is categorised under “assessment in individual cases” (yellow) is the legal situation with regard to composting in Germany and/or the lack of a recycling system, and not the end-of-life options offered by the manufacturers.
All NatureFlex™ films are certified according to DIN EN 13432 and therefore suitable for industrial composting. They are also certified according to the OK compost HOME standard of TÜV Austria for home composting.
In practice, however, the film is sorted out in many German composting plants and then transported to the waste incineration plant.
Some films are suitable for anaerobic decomposition and marine biodegradation.
The DIN EN 13432 standard also prescribes tests for heavy metals and ecotoxicity to ensure that the materials do not have any toxic effects or influence the quality of the compost. Futamura also tests the plasticisers used. Ecotoxicity tests are carried out with cress and spring barley, as these are the standard tests for meeting this requirement.
Mixing a paper fraction with NatureFlex™ films appears to be unproblematic. A study indicates that paper laminates with NatureFlex™ can be recycled in a paper mill. According to the company, it is being investigated whether this can be implemented in practice with a short reaction time of 15 minutes, which would have considerable advantages. However, films are generally not recycled. Further information can be found here.
According to Clarifoil, more than 99.5 percent of the acetone used in the process is recycled. Leftover quantities of the standard transparent film, which are generated during the production process, are recycled. Clarifoil is certified according to the following systems: DIN EN 13432, ASTM D6400 and Vinçotte OK compost HOME.
According to the FKuR, the in-house recycling of production waste or rejects is straightforward if they are properly separated according to type. Depending on the application, up to 50 percent regranulate can be added to the new material. Some Biograde® types are certified according to DIN EN 13432 and ASTM D6400 and are therefore considered compostable materials (industrial composting).
A Life Cycle Assessment (LCA) for NatureFlex™ exists but is not publicly available. Futamura is available for specific questions. In 2014, a gas turbine was installed to generate energy in-house. Initial data confirm that the energy efficiency of production has improved as a result. The existing LCA will be updated as soon as sufficient data is available.
Currently, according to Futamura, the CO2 footprint for NatureFlex™ is higher than for PP film, but lower compared to PET film. However, it will improve within the next two to three years as modifications are made to the plant and the technology. NatureFlex™ film is considered a replacement for PET film due to its heat resistance properties. Further information can be found here.
Innoviafilms, a company whose cellulose business activities have been integrated into Futamura Chemical Co., Ltd. since 2016, stated that the company was able to assess the environmental effects of various laminate structures (conventional and bio-based) using an in-house CO2 assessment tool. The tool (developed by PE International, based on GaBi software, cradle to gate) is integrated into a “sustainability wheel” to provide a picture of the four most important aspects for Innovia: raw material, process, packaging performance, end of life.
Regenerated cellulose and cellulose acetates contain different percentages of bio-based materials.
Futamura
The company states that the bio-based carbon content of NatureFlex™ films (regenerated cellulose) is between 90 and 95 percent according to ASTM D6866. A small amount of additives is used. The plasticisers used do not contain phthalates and are not toxic.
Clarifoil
According to Clarifoil, about 60 percent (by mass) of the C content of their films is bio-based. The polymer (cellulose) itself is 100 percent bio-based. The bio-based content is reduced by the modification into acetate. For cost reasons, synthetic acid (concentrated vinegar) is used instead of organic acid.
FKuR
According to FKuR, Biograde® (compounds based on cellulose acetates) is more than 50 percent (by mass) bio-based.
2. Social compatibility

The assessment must be specific to each production area.
Futamura
The company Futamura is FSC and PEFC certified. Futamura supplies the USA and Great Britain, among others. The certifications for forest management and product chain certification are based on the ILO standards for FSC and PEFC.
The manufacturers of cellulose-based plastics produce in Europe and the USA. This means that the European and/or American social standards apply.
The company is certified according to FSC and PEFC in both producing countries – the USA and Great Britain. The certifications for forest management and product chain certification are based on the ILO standards for FSC and PEFC.
Social standards for the processing of Clarifoil are covered in the 2018 Annual Stewardship Report.
A certification of FKuR according to the code of conduct of the German Association of the Plastics Converters (GKV) is available.
3. Safety and technology


Currently, only very few cases of migration potential for cellulose are known. There are references to diethylene glycol (DEG) in the literature, for example.
If labels are used, the migration potential of the adhesives also needs to be considered.
The raw material additive anthraquinone was used in the paper industry outside Germany, which led to residues in various products packaged in paper. There is a recommendation from the BfR (German Federal Institute for Risk Assessment) on this issue: No. XXXVI (“Paper Recommendations”).
There is very extensive data on cellulose and the materials made from it. This information can be found for instance in the Biopolymer Bank as part of the “Material Data Center”, which was created by IfBB Hannover and the company M-Base with the support of the Federal Ministry of Food and Agriculture (BMEL).
The packaging material NatureFlex™ is intended for use in the food sector and has a good mineral oil barrier.
The Futamura website provides comprehensive information on the application possibilities. There are numerous possible applications for cellulose packaging. Due to the wide range of possible applications, we recommend contacting the manufacturer directly to obtain an assessment of whether the material is suitable for the desired applications.
For films:
If additives are used to prevent fogging, the conformity of these additives must be checked, as they are surface-active. The additives can only be applied as a surface coating. During processing, the static charge of the films must be taken into account and reduced via mechanical precautions. Good results have been achieved with water-based coatings. For laminates with cellophanes, glycerol esters and metal salts which comply with FDA guidelines are used.
For containers:
For special product applications, containers can be made of cellulose derivatives. This has rarely been done so far.
Processing can be carried out on traditional processing machines. Most cellulose packaging materials have sufficient stability even at higher production temperatures.
Biograde® can be processed with standard injection moulding machines. Processing in a hot runner is possible. However, as bioplastics can degrade if left under high temperatures for too long, a prior technical consultation from the manufacturer is recommended. Packaging made of Biograde® can be printed on (laser, offset, hot foil stamping) and can be coloured in a variety of ways using masterbatches.
Unfilled packaging should be stored dry, cool and not longer than six months.
Packaging materials containing cellulose are unproblematic in processing. The printability of the films is very good.
Cellulose has good barrier properties against fat and mineral oils due to its molecular structure. However, cellulose has a very high water vapour permeability and low barrier properties against oxygen and carbon dioxide.
Many required material properties can be achieved via the appropriate lamination or other functionalisation processes.
The applications of cellulose can be expanded through constant further development.
4. Quality


You will find the general legal requirements for food packaging here. There are legal regulations for plastics and cellulose (regenerated cellulose, cellophane). In addition, the German Federal Institute for Risk Assessment (BfR) has provided recommendations for the test methods in the database “Methods for testing paper and board for food contact”. Furthermore, there are recommendations for printing inks and general recommendations regarding packaging requirements.
Untreated cellulose packaging offers a high water vapour permeability (200–400 g/m2*d according to DIN 53122) with barriers for oils, fats, water and mineral oils.
As can be seen from data sheets, cellulose packaging offers significantly better aroma protection than polypropylene packaging. The packaging is therefore ideally suited for fresh products and baked goods with a shorter shelf life, in particular for tea, coffee, chocolate and pasta.
Due to the transportation of moisture, these types of packaging are only suitable for products that do not require a water vapour barrier (e.g. chocolate).
Due to their very attractive appearance, cellulose packaging is used more frequently for designer products (e.g. fashion and perfume products). In addition, thermoplastically processable cellulose derivatives can be used for injection moulding and film extrusion applications.
Today, cellulose derivatives are only used to a limited extent outside the food packaging sector (films for envelopes, filters, consumer goods and cosmetics packaging).
Cellulose packaging is used for packaging spices, tea and tasting bags, as well as various dry products. Compostable fruit and vegetable nets made of cellulose fibres are also in use. The packaging material is also used as a freshness seal or as a seal closure, which guarantees the authenticity of a product. If customers have very high optical expectations for a particular packaging with regard to gloss, cellulose packaging is a very good choice.
Due to their good optical quality, cellulose packaging is the ideal packaging when high expectations need to be fulfilled regarding the appearance of the packaging.
The film is relatively stiff (more brittle than PE) and has a high gloss with good adhesive properties for adhesives. The manufacturers (Futamura, Clarifoil, FKuR) provide detailed information on sealability and printability.
Cellulose packaging has a very high mechanical stability. However, the very brittle material can break when exposed to heavy stresses.
Strongly fluctuating moisture levels in the ambient air are particularly problematic. Such fluctuations can cause packaging deformations (undulation). As a result, the coatings may no longer fit tightly, causing visual defects. Therefore, very dry ambient conditions are an essential aspect for the storage of the packaging material.
Compared to other bioplastics, this family of materials has some outstanding properties, e.g. the high heat deflection temperature of over 100 °C, the chemical resistance and the low inherent odour. There exist greatly varying material types which have been optimised for the respective areas of application.
There are also applications for cellulose foams.
Further exciting developments can be expected modification possibilities of the cellulose molecule.